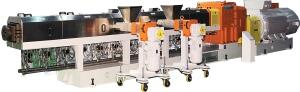
Icma San Giorgio hosts a three-way open house along with its partners Filtec (from Italy) and Ettlinger (from Germany) at its offices in San Giorgio su Legnano, near Milan, on February 19-20. The three companies play a leading role in their respective fields: recycling-compounding, filtration systems and cutting devices. Three innovative systems will in fact be presented which, when working in combination, recycle heterogeneous waste, based on three factors considered to be fundamental: innovation, profitability, differentiation.
Two live demonstrations will be given during the open house on a line based on Icma San Giorgio's co-rotating twin-screw extruder, which is technologically state-of-the-art and optimized for advanced recycling. The first demonstration will involve the processing of highly heterogeneous packaging waste, including primarily polyolefins, but also containing barrier film, metal film, printed film and so on. Normally because this type of waste is not uniform, it cannot be recycled or it is used to make low cost products, such as low-pressure mouldings. The extruder used, on the other hand, gives the product a high added value in order to obtain a material that can be used in more sophisticated applications.
The second demonstration also intends to offer an almost extreme example of recycling, namely ground but not washed car bumpers. Normally these components are polypropylene, with thermoplastic rubber additive to increase the elastic modulus and with mineral fillers to boost sturdiness. The co-rotating twin-screw extruder provides certain advantages that permit maximum extraction of the volatile substances from a matrix of this kind: in addition to mixing heterogeneous materials, in particular a degassing system has been installed that is much more efficient than other technological solutions. The co-rotating technology also offers the exclusive opportunity of filling or reinforcing the polymer, to obtain (although this aspect was not part of the demonstration) an even more attractive produce in terms of profitability.
A continuous, latest generation ERF filter change developed by Ettlinger is installed downstream the extruder. The device is fully automatic and reaches extremely high filtration performance levels, to the order of 650 micron, even with a very high percentage of pollutants and without requiring the constant presence of an operator. Further downstream, the line will have an submerged cutter, developed by Filtec specifically for this process. The submerged technology used will permit cooling of the material immediately on output from the line, thus guaranteeing highly precise grinding even with highly complex materials.
The event programme is as follows:
10 a.m. - Registration
10.30 a.m. - Welcome speech (G. Colombo, Icma San Giorgio)
10.40 a.m. - Why use co-rotating twin screw extruders in recycling (C. Moneta, Icma San Giorgio)
11 a.m. - Continuous ERF filters, high filtration technology (I. Talenti, Ettlinger)
11.20 a.m. - The cutting quality of recovered materials (A. Baracco, Filtec)
11.40 a.m. - Demo with recycling of post-consumer waste from bumpers
12.30 p.m. - Lunch
2 p.m. - Recycling demo of post-consumer packaging film waste
3 p.m. - B2B meetings