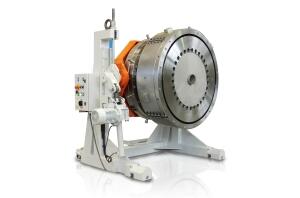
The Venus 3000 and Venus 2000 die heads were developed by Tecnomatic for the high-performance extrusion of pipes with diameter from 710 to 2600 mm. The line configuration includes two extruders with a capacity of at least 1 ton and provided with a capacity adjustment system. The extruders are synchronised and the output rate is set by weight/metre. This solution increases the line performance and ensures short delivery times as a result of the high production capacity. The design of Venus 2000 and Venus 3000 die heads is based on two spiral distributors incorporating the same flowing channels adopted for the other die heads of the Venus range. A short and simple preliminary melt distribution section for each distributor makes it possible to obtain a wide opening in the head's centre for internal pipe cooling. As a result, the feed points of the extruders are arranged horizontally to the left and right of the centre opening, while the extruders themselves are placed in parallel though remaining easily accessible.
All Venus models are engineered in such a way as to allow internal pipe cooling. The basic head, the adaptations and the mandrels ensure that the pipe is insulated right up to the head, so that the inside air can be evacuated. This guarantees several advantages. In terms of product, a better distribution of the inner strain is obtained thanks to uniform cooling, as well as lower shrinkage at the end of the pipe after cutting and reduced thermal stress on the inner surface, which ensures a longer life for the products. As regards investment costs, the internal pipe cooling feature requires fewer cooling tanks, shortening the corresponding section of the line up to 40% as a result decreasing the associated costs. In terms of operating costs, the energy requirement is lower for the cooling water circuit pumps and the spray tank recirculation pumps, as well as for process water cooling. In addition, start-up time are faster, and the cycle times shorter, since the line is more compact.