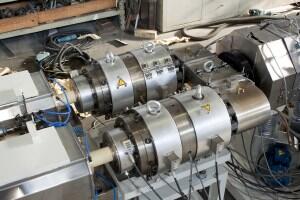
Bausano's technological evolution in 2013 moved along two main lines: energy savings and machine ergonomics to allow easier use by operators. The PVC pipe and profile extrusion lines were completely redesigned, with the company choosing not to optimise the machines belonging to the previous generation, which were already more than a decade old, but rather to develop new products offering certain innovative features.
The new profile extrusion lines guarantee 30% and 80% reductions of energy and water consumption, respectively, which, for the same quantity of raw materials used, are the two areas where it is possible to intervene in order to reduce the final cost of the product. To make these lines easier to use, the company has developed a highly advanced joystick-operated sizing system, which allows the operator, from a single workstation, to adjust all the movements of the sizing die holder. The system is designed to make for easier machine operation, even by operators who have received little training.
For the sector of pipe production, including large pipes, the company has developed double-outlet extrusion lines which can double the output of a single extruder and a single belling machine. In this case, the energy savings are even greater than those that can be obtained in profile production. By means of a particular electronic modulation of the pumps the energy consumed by the last part of the line can be reduced by as much as 40%. This is a remarkable result, whose effect is to reduce the cost of the product.