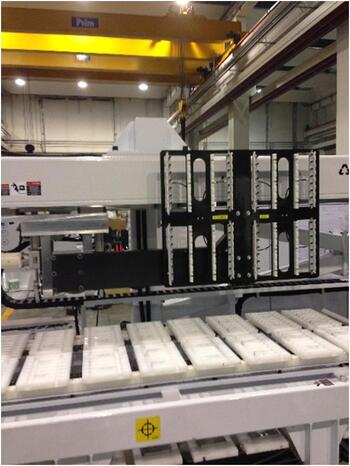
2014 sees Star Automation Europe celebrating 25 years in business, a milestone that coincides with the fiftieth anniversary of its parent company Star Seiki. This important achievement has been marked by the development of an automated system for the production and packaging of disposable cutlery. It has been an important experience for the company as it initially appeared to be a difficult undertaking, not least from a financial point of view. It was immediately clear, soon as the basic layout had been worked out, how much space the system would need and what it would offer in terms of technological content.
The development of the project, conducted in collaboration with the processor and with the injection moulding machine manufacturer BMB, led to the creation of what can be considered the only system in the world that is able, without any supervision, to produce disposable cutlery and package it either in individual sets, with or without a napkin, or in packets of 25, 50 or 100 pieces for large retailers. Indeed, in the course of each cycle, lasting 6.5 seconds total, it is possible to change the finished product packaging mode, without having to replace the 64-cavity mould or any parts of the automation system, such as the store and grippers, and without even having to turn off the machine. All you have to do is change the machine’s operating program.
The 550-ton BMB eKW55pi machine, equipped with the processor’s own mould for producing 32 forks and 32 knives, turns out 590 pieces a minute, which adds up to 849600 items a day. The side entry robot picks up the moulded articles and deposits them on a motorised rotary table or on a transfer line ready to be packaged individually or in pairs with a napkin. Whereas the packaging in multi-pack function did not even need to be tested, the packaging of the items individually or in pairs needed more careful attention, given that the time available for the handling and packaging of one piece was just 0.1 seconds. The solution was found thanks to the integration of vision systems that were directly interfaced with a high-performance Scara robot, produced by Staubli: the Cognex vision system monitors the product position, number and type and, in infinitesimal fractions of time, transfers this information to the robot. The robot picks up the single item of cutlery and deposits it on the napkin, which has already been selected as appropriate and placed on the feeding belt of the flow pack machine produced by Schib Packaging, a long-standing partner of Star Automation Europe.
This smart system can handle up to 600 pieces a minute, packaged individually, in pairs (knife and fork), and with or without a napkin included in the package. One of the greatest difficulties encountered was, without doubt, the need to find a way of “peeling off” the napkins, since these can often vary greatly in shape and consistency, thereby presenting problems for traditional handling systems.
A crucial aspect, as regards this system, was certainly that of achieving the perfect software calibration between the vision system and the anthropomorphic robots. It was a case of ensuring the conveying of complex information, at an extremely high speed, between two pieces of equipment that do not normally interact, but that in this case were responsible for the outcome of everything that was going on around them.
Recently installed in northern Europe, this system stems from Star Automation’s experience and technological excellence, from an enormous amount of work and from the value, also in economic terms, that was attached to it. The start-up coincided with Star Automation’s 25th anniversary.