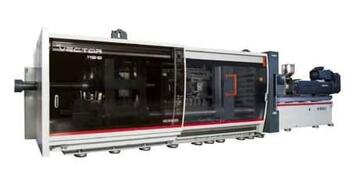
Negri Bossi has exhibited five fully-integrated injection moulding machines at Plast 2015, focusing particular attention on energy consumption.
The company showcased a 1100-ton machine from the eVector series in the “automotive” configuration for moulding PMMA headlight frames, with pick up carried out by an anthropomorphic robot developed by Comau, and automation developed by MGM.
The eCanbio series with a SmartFlex mould clamping unit and Smart Energy hydraulic system was also on show. The e180 machine is dedicated to the moulding of a snorkelling mask using three materials. The whole system, developed in cooperation with Guzzini Engineering, allows a complete product to be achieved through the addition of LSR without post-production processing. Thermoplastic injection, PBT with additives to better adhere to LSR, is made using the main injection unit, which has reduced dimensions to permit the injection of only 13 grams of the frame without degradation of the polymer. Once the thermoplastic resin is injected, there are the three injections of LSR thanks to an injection system directly integrated on the mould: the first one is for the injection of the lace of the mask, the second one is for the injection of the lens using a specific silicone grade for optic applications and, finally, the third is for the injection of the seal of the lens through a tank of silicone and nitrogen.
The e250 HE machine was presented with an elegant moulding system called Extreme. It was equipped with a Siemens torque electric motor in the plasticising unit. The eCanbio HE machine permits the complete overlapping of movements allowing in many cases an increase in the performance and optimisation of the cycle time. With Industrial Frigo, the heat&cool technology shown at Plast is a perfect balance within the injection process for producing technical and aesthetic parts. The moulded item consisted of an ABS grille for espresso coffee machines, particularly representative of this type of technology.
The stand would not have been complete without multi-material injection presses, also equipped with SmartFlex clamping units, with prismatic guides to control the highly refined and precise opening and closing speed, creating an oil-free mould zone. The eCanbimat 330 with vertical injection unit and Smart Energy hydraulic system was equipped with a mould for a little folding box in two colours. The moulding technique allowed the perfect balance of the two colours. The magnetic platens supplied by Rivi ensured reliability and meet the production need of frequent mould changes. The e500, also in Smart Energy version, was equipped with a two-cavity mould for a component for vehicles in polypropylene and thermoplastic rubber. The rubber injection was made by an independent injector connected directly to the mould.
All the automation present at Plast were manufactured by Sytrama who presented their complete range of robots and the new SCP2 touch screen at the show.