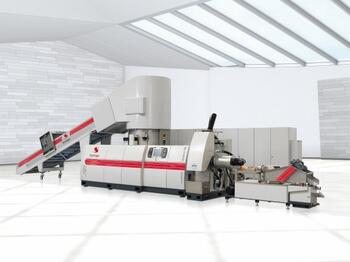
The recent “Dynamic Days”, hosted at the Starlinger’s technical centre in Weissenbach, Austria, were organised by the company to present the its latest technological developments in plastics recycling following the recent launch of the recycling line recoSTAR dynamic, and to mark the relaunch the recoSTAR universal series. Three different recycling lines were up and running in the newly refurbished technical center of Starlinger recycling technology. On a recoSTAR dynamic 105, equipped with the high-performance C-VAC degassing module, heavily printed LDPE film and humid LDPE film contaminated with paper were processed. Transparent stretch film was recycled on a recoSTAR dynamic 65 line, and woven PET fabric production waste on a recoSTAR universal 65 VAC recycling line.
Highly automated operation and continuous process adjustments on the recoSTAR are now possible using the Dynamic Automation Package. This allows to increase the machine uptime and productivity of the recoSTAR dynamic while reducing the overall energy consumption by up to 10 %. The recycling line automatically starts up and shuts down via the SmartStart feature, and when the material feeding is stopped, the SMART feeder switches into stand-by mode without requiring operator interaction. The automatic temperature controller allows the processing of input materials with different moisture levels and varying bulk density, all the while maintaining consistent product quality.
The increased capacity of the large Smart feeder results in a much larger operating window, while the self-regulating material feeder allows the extruder to process a wider range of input materials, giving recyclers greater flexibility in the marketplace. Additives can be fed directly into the extruder through a side feeding unit while the output feedback loop ensures total process control.
Energy savings are achieved using the new extruder drive concept as well as the use of motors classified IE3 or NEMA Premium (highest efficiency standard according to the U.S. National Electrical Manufacturers Association), as well as the use of infrared heaters on the extruder barrel. The use of the radiant heat of the extruder for material processing helps to recover additional energy.