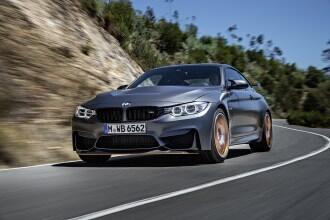
During the exhibition JEC World in Paris (March 8-10, 2016) Solvay launches its new rapid cure thermoset resin system MTR 760, which BMW selected to manufacture the CFRP hood of its new M4 GTS.
This new resin system was specifically developed to manufacture resin impregnated carbon fibre blanks through processes such as filament winding. It offers very good processing properties with rapid cure, a DMA onset TG of 135°C, superior toughness and it has excellent dynamic loading characteristics. The outstanding surface finish of the resin allows a Class-A paint finish.
In search of an effective CFRP lightweighting solution, MTR 760 filament wound prepregs have been selected for this application. “Solvay developed a new thermoset resin to meet BMW’s technical and commercial requirements for performance and cycle time enabling them to introduce a CFRP hood structure on their new M4 program”, said Manfred Duri, Automotive Business Development manager Germany, of Solvay’s Composite Materials global business unit.
Solvay’s commercial and application engineering team worked very closely with the supply chain C-Con (development, tooling and system supplier) and Läpple (pressing and bonding), from the start of the vehicle program, to ensure that the material and manufacturing process were optimised, from design for manufacture, product development, to automated serial production. This gave the opportunity for short-term adjustments of the resin system while still meeting the project timeline.
“We are proud of our team and our close partnership with Solvay, which enabled the development of this new resin system and the corresponding manufacturing process within only 9 months. All development goals of this CFRP hood, e.g. dynamic load conditions or Class-A surface have been achieved through a close coordination between C-Con and Solvay’s Technology and Process Engineering teams”, said Michael Neuner, general manager of the German company C-Con.
“To meet customers’ needs in lightweight material solutions, CFRP has become a major R&D field at Läpple Automotive. With Solvay and C-Con we have two strong partners, with great expertise in their field of serial production processes”, said Oliver Wackenhut, managing director, Läpple Automotive (Germany).
The press moulded hoods are manufactured using a Double Diaphragm
Forming process with tailored composite blanks. Diaphragm forming offers
multiple advantages, including blank support during the pressing process, which
eliminates the need for preforming as well as more cost effective, simplified
tooling which is a clear investment benefit. The Double Diaphragm Forming
process gave Läpple the opportunity to capitalise on their sheet metal know-how
and to apply it to forming CFRP parts.
The films used for this process are proprietary to Solvay and are matched to the resin system to offer the right level of conformability to the tool geometry. A hood will be on display on Solvay’s booth at the upcoming JEC World and at the VDI conference and exhibition Plastics in Automotive 9-10 March 2016 in Mannheim.
Solvay’s new global business unit Composite Materials - which combines the former Cytec Aerospace Materials and Industrial Materials businesses - is a global provider of technologically advanced lightweighting material solutions that enable companies in the aerospace, automotive and other demanding industries to design, develop and efficiently manufacture high-quality, high-performance and complex composite structures. Composite Materials has one of the most extensive product portfolio, including prepregs, resin systems, adhesives and surfacing films, carbon fibre, textiles, tooling and vacuum bagging consumables.