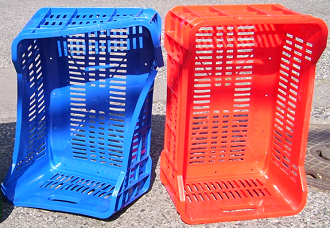
Ampacet has recently developed two new ranges of masterbatches in order to help processors to optimise the production and delete products shrinkage and warpage. These phenomena can occur in particular during injection moulding and blow moulding.
Shrinkage is the dimensional reduction brought about by the decrease in volume of the moulded material as it cools and solidifies. Warpage is a distortion where the surfaces of the moulded parts do not follow the intended shape of the design, and it is due to differential shrinkage in the machine and transverse directions because of a non-uniform cooling of parts with wall sections of varying thickness and a presence of some pigments that affect the polymer crystallization.
Shrinkless 057 1000057-E has been created for polyethylene-based products and Shrinkless 106 4000106-E has been developed for polypropylene-based products to help reduce the distortion phenomenon. Benefits of these masterbatches for injection moulding and blow moulding include:
- dimensional stability, reducing the impact of high shrinkage colours
- no process modification needed or expensive tool adjustments to run the different coloured parts on the same mould
- help for moulders to minimize warpage when running a part that calls for the successive use of different colours
- minimum deformation during mould release
- product flexibility (effective on a great variety of masterbatches)
- better cap fitting
- shorter cycle times (greener process)
- food contact approval (EU)
- no impact on the colour of the final article.