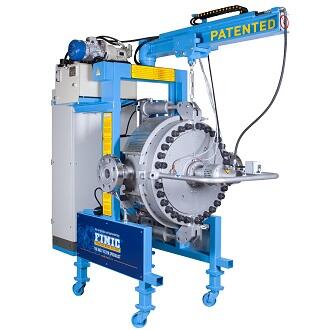
Family business specialising in the production and maintenance of fire protection systems, the Italian company Italfire is headquartered in Manduria (near Taranto, Italy). It recently entered the plastic recycling market when Antonio Lodedo, the owner, and his son Matteo installed a recycling line for post-industrial and commercial LDPE, entirely made in Italy.
As part of this project, Fimic had the task of improving the filtration quality of washed plastic material with high contaminant content. Italfire required a technology that could process wood, PET, paper and other plastics. The contamination level is around 4-5%; however, as it often happens, the contaminants entering the extrusion process can vary considerably.
For this reason, the mesh screen could not handle such levels of contamination at full production without the risk of failures and, above all, of high spare part costs. To counter these problems, Fimic delivered a RAS 700 screen changer with a filtering surface of almost 4,000 sq.cm and a single laser screen, adapted prior to shipping, so that flanges and height could fit the customer’s extrusion line. This allowed the user to replace the existing filter screens halting the machine for one day only.
The laser technology allows the production of 1,500 kg/h of quality LDPE film with a 150-micron screen. In addition, the 5% contamination is eliminated from the recycled plastic and the waste, containing a minimum percentage of contaminated plastic, is reprocessed with a 400-micron screens in order to obtain a material fit for injection moulding.