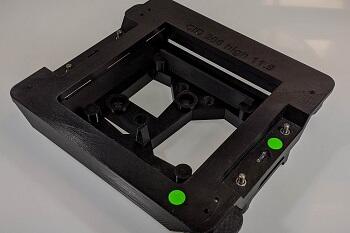
Renowned as one of the world’s leading tire manufacturers, automotive technologies leader Continental actually has an even wider solutions portfolio, including automotive part production, connectivity, automated driving and mobility services via its Continental Engineering Services (CES) division. Cost effectiveness and speed are keys to its manufacturing success, and that’s turned the company on to effective use of additive manufacturing.
Continental has its own Additive Design and Manufacturing (ADaM) Competence Center, which offers both internal and external customers a wide range of additive samples, mechanical parts and series production solutions with metal or plastic assemblies. Continental’s ADaM Competence Center houses an industrial-grade FDM-based Stratasys Fortus 450mc 3D Printer, which manufactures final production parts, prototypes and - most notably - jigs and fixtures for the company’s own production line machinery.
Key to the company’s production capabilities is a range of specialized additive manufacturing materials, enabling the team to produce customized solutions for the production line - such as Stratasys’ Ulyem 9085 resin and ESD-compliant ABS ESD7.
When producing automotive parts and solutions for customers, Continental Engineering Services works with multiple electronic parts and components on its manufacturing floor. Static dissipative properties are therefore paramount for all machinery parts that come into contact with electronic components. This prevents static discharge, which could damage products, impair performance or even cause an explosion or fire. For the many fixtures and tools manufactured in-house at Continental, ABS-ESD7 material meets the necessary electrostatic discharge standards for handling sensitive electronic parts - while also offering durability and stability. Automotive displays are one such application.