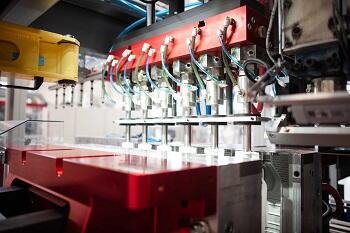
AlphaMAC has developed its range of blow-moulding machines starting from the knowledge acquired from the previous experiences of two generations of electric machines and presents itself on the market with a very advanced technology regarding consumption.
One of the most current and important aspects with the evolution of technologies in the field of extrusion and blow-moulding is certainly the reduction in electricity consumption, obtained thanks to the conversion of the motion from hydraulic to electric. Begun in 2006, this transformation has led today to have extremely reliable and repetitive machines, reducing drastically the maintenance linked to hydraulics (about 65% less), also eliminating the environmental impact linked to the periodic disposal of oil, and with a greater flexibility in process regulation, having many more controllable parameters available.
The surveys carried out on machines in production confirm that the average electrical consumption achieved is much lower than it was on hydraulic machines, in particular when the machine is used at its maximum capacity if we consider the consumption per kilo of extruded plastic. In fact, the most important part of consumption is linked to the heating of the resistances that keep the extruder and extrusion head at the set temperature, regardless of how many kilos the user transforms.
In a practical case, we can see how an ALPHA 800D machine, with double station, has an extremely low consumption.