Innovate to produce better and reduce costs
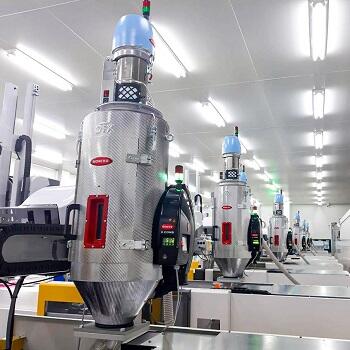
“Plastic products are essential in our everyday life” says Renato Moretto, founder and President of Moretto, manufacturer of auxiliary equipment for the plastics industry. “Our real challenge is to turn the critical issues related to plastics mass production into opportunities for the future.”
The company’s approach to R&D and product development has been highly innovative for many years. Any new project is driven by the idea of using plastics in a smart way. That is why Moretto is a strategic partner for high technology businesses such as the aeronautical, the medical, and the automotive industries. The general trend in these applications is developing products which perform increasingly better and therefore require less energy.
Plastic resins used for producing high-tech products require special care during the transformation process, starting from the very first steps of the production cycle. External factors such as the ambient temperature and moisture greatly affect the end result, therefore a system which ensures consistency and stability is absolutely crucial to generate high quality products as well reduce energy consumption.
“Our mission is to develop innovative products which meet our customers’ most demanding expectations”, Renato Moretto adds. “The only possible approach to today’s global market is sustainable profitability.”
The X Comb mini dryer is a super compact system which guarantees excellent manufacturing performances regardless of the external ambient conditions. The full electric X Comb dryer is specifically designed for technical plastic materials. Its outstanding performance is achieved through innovative design features such as the honeycomb desiccant rotor with molecular sieves made of zeolite 100%, one of the most efficient moisture absorbent in the market. The dryer’s “adaptive” feature ensures a very gentle and consistent polymers treatment with dew point levels up to -52°C. Two variable flow turbo-compressors only supply the required airflow optimizing the energy consumption. The original OTX (Original Thermal eXchanger) hopper can reach efficiency levels which are unique in the drying equipment market.
X Comb was designed using advanced thermodynamic simulation software, a modern approach which helps reaching incredible product performances and at the same time shortens the product time-to-market.
“We always focus on another important aspect, the operator safety”, Moretto continues. “Companies are made of people, and people need to be able to work safely and efficiently. Simplicity and practicality are the basics when dealing with industrial automation systems”. X Comb is equipped with an assisted lid and safety device which enable the operator to carry out inspection and maintenance procedures in a very easy and safe manner.
The LCD touch screen is a standard built-in intelligence feature that only requires two parameters - the type of material and throughput - all the other parameters are automatically set. The interaction between the operator and the system is extremely easy thanks to the graphic user interface.
“All modern manufacturing processes are data-driven. Our dryer includes multiple connectivity options such as RS485, Modbus and USB for data downloading. It also can be connected to Mowis, our supervision and management software which enables connectivity between different systems, processes, plants and even facilities”, Renato Moretto concludes.