One cross head for two extrusion lines
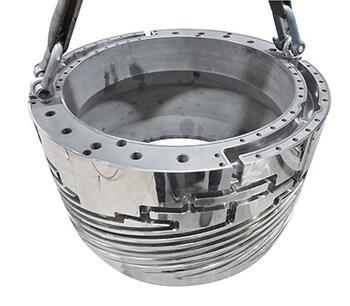
The company Conextru managed a project and designed a cross head which can be moved in between two extrusion line for PE pipes coating with PP. The special request for that cross head was to cover the big diameter range from 63 to 500 mm on two different extrusion lines. Line one covers the range from 63 to 250 mm and line two from 250 to 500 mm. This was managed by add on system for the die sets. One die set is foreseen to cover three outer diameters. To make this possible, the extruder for the PP layer is placed in between the two extrusion lines. To be able to feed the cross head just with one extruder, a special turntable and changeable adapter was designed to reach always the same feed point of the head, which is on top of the cross head. The system for coating includes a preheating station at backside of the cross head. This heating system is based on IR emitters. The are four temperature zones which are adjustable in temperatures. This unit can cover the same range of pipe diameters as the head (63-250 mm and 250-500 mm). Preheating increases flexibility of the process because a certain surface temperature of the PE pipe is needed in order to get the required adhesion. On the other hand, the pipe itself should be cold for the coating to get nearly same shrinkage of both materials, PP and PE. Both units are mounted on one frame and the frame runs on wheels to shift easy from line one to line two. The head itself is based on helical spiral distributor, a well-known proven system for best melt distribution. The head has low volume and small channels for the lower output range suitable for PP and PE. The head is heated from outside as well from inside. For smaller pipe sizes, there is a pipe support to make sure that the pipe is kept straight in the head for best uniform coating.