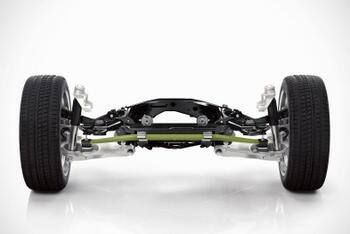
I compositi rinforzati con fibre di vetro o di carbonio associano risparmi di peso - che permettono di ridurre il consumo di carburante e le emissioni di anidride carbonica - a un’enorme robustezza, offrendo quindi maggiore sicurezza e buon comportamento in caso di collisione. Per questo Henkel lavora in stretta collaborazione con le aziende per creare soluzioni su misura e integrate, in risposta alle sfide poste dalla costruzione leggera nel settore automobilistico, con particolare riferimento all’efficienza energetica e all’idoneità per le produzioni su vasta scala.
Nell’ambito della propria collaborazione con Benteler-SGL (primario produttore di componenti in composito per il settore automobilistico), rivolta allo sviluppo e alla produzione su larga scala di una balestra in composito per Volvo Cars, Henkel ha contribuito in particolare con il suo know-how relativo al processo RTM (Resin Transfer Moulding), in modo da ottimizzare ulteriormente i tempi di ciclo.
Per la sua bassa
viscosità, la matrice poliuretanica della resina Loctite MAX 2 di Henkel
riempie velocemente lo stampo, impregnando rapidamente e delicatamente la fibra
e consentendo tempi d’iniezione più brevi. Grazie alla velocità di reticolazione
notevolmente più elevata rispetto alle altre resine epossidiche, riduce inoltre
i tempi complessivi del ciclo. Loctite MAX 2 è stata usata con successo nella
produzione in grandi serie di balestre sin dal 2013. Inoltre, il progetto
attuale utilizza additivi selezionati, che rendono più veloce e flessibile la
fase di reticolazione.
Le sospensioni della nuova Volvo XC90 offrono la caratteristica innovativa di balestre trasversali in composito rinforzato con fibra, al posto delle tradizionali molle. Questo permette un design molto compatto e consente inoltre un risparmio di peso di circa 4.5 kg, rispetto alle convenzionali molle. Ulteriori vantaggi funzionali sono una guida più fluida e un miglioramento nelle prestazioni NVH (rumore, vibrazioni, durezza). Il volume del portabagagli è anch’esso maggiore, perché vengono eliminate le torrette degli ammortizzatori. Volvo funziona con il principio denominato “Architettura a Piattaforma Scalabile” (SPA), in base al quale alcuni concetti implementati con successo vengono adattati in modo flessibile ad altri modelli di auto. Il nuovo assale posteriore è quindi destinato a essere incorporato in nuove automobili negli anni a venire, ossia parecchie centinaia di migliaia di veicoli all’anno. La nuova Volvo XC90 rappresenta quindi solo l’inizio.
“L’esempio
della nostra balestra per Volvo Cars dimostra che la produzione di massa di
compositi a base fibra è già una realtà di oggi. Inoltre, con la flessibilità
che essa consente nella progettazione di componenti, siamo in grado di
soddisfare il fabbisogno di balestre di una intera piattaforma di modelli con
un relativamente piccolo numero di varianti. Avendo un partner come Henkel,
siamo stati in grado di sfruttare la nostra esperienza per ottimizzare
ulteriormente il livello di automazione applicato nella nostra attività di
produzione di compositi. Questo progetto dimostra che il nostro concetto di
balestra leggera è idoneo non soltanto per veicoli commerciali, ma anche per
automobili. Riteniamo anche che la tecnologia poliuretanica di Henkel offra un
grande potenziale per lo sviluppo di ulteriori applicazioni automobilistiche”,
afferma Frank Fetscher, responsabile del Business Development di Benteler-SGL
Automotive Composites.