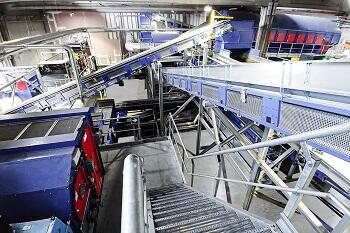
Con la scadenza dell’agenda 2030 sempre più vicina, le società per i servizi ambientali inseriscono sempre più spesso nei propri piani industriali investimenti in impianti di riciclo in grado di avvicinarci sempre di più all’obiettivo zero scarti, trasformando i rifiuti in materie prime seconde in grado di essere reimmesse in commercio di generare a loro volta scarti ridotti al minimo. In quest’ottica, Stadler è stata scelta da Gaia e da Iren Ambiente (che detiene il 45% di Gaia e serve oltre tre milioni di abitanti nel settore dei servizi ambientali) per realizzare i loro nuovi impianti di riciclo ad Asti e a Parma, rispettivamente per la selezione degli imballaggi in plastica provenienti dalla raccolta differenziata e la selezione di plastica e carta/cartone.
Il nuovo impianto di Asti per la selezione di imballaggi in plastica e metalli da raccolta differenziata è frutto di un investimento di 10 milioni di euro e consentirà di trattare 50 mila tonnellate all’anno di materiale. Questo, una volta processato e ripulito, sarà consegnato ai consorzi nazionali per il recupero degli imballaggi che provvederanno a trasformarlo in materie prime seconde e reinserirli nei cicli produttivi. Il nuovo impianto è dotato di moderne tecnologie in linea con gli obiettivi dell’Industria 4.0 e le macchine vanno ad affiancare il lavoro degli operatori addetti alla cernita manuale, ottenendo come risultato un prodotto in uscita dalla qualità elevata.
In dettaglio, l'impianto è composto da una sezione di alimentazione e preselezione, una linea di selezione meccanica e ottica, una cabina di cernita per la selezione manuale dei prodotti più ingombranti e una linea di stoccaggio e imballaggio. La prima selezione viene effettuata da un vaglio rotante che suddivide il materiale in base alla dimensione in tre flussi. Il flusso di materiale principale, con pezzatura da 50 a 350 mm, viene inviato alla linea di selezione principale, composta da: dieci 10 separatori ottici per dividere diversi polimeri plastici; un sistema di separazione ad aria per migliorare la separazione delle frazioni 2D e 3D; due separatori magnetici per la rimozione dei metalli ferrosi; un separatore a correnti parassite per estrarre i metalli non ferrosi; un vaglio fine con maglia da 20 mm per separare i residui fini; un separatore balistico STT5000 e uno STT2000 per aumentare la qualità del ricircolo della plastica all'interno dell'impianto; un perforatore di bottiglie per recuperare i contenitori in caso siano pieni di liquidi. Tutta la plastica selezionata viene prima accumulata all’interno dei bunker di stoccaggio e successivamente alimentata a due linee di pressatura indipendenti, caratterizzate da speciali presse progettate per la plastica. Alla fine, il materiale in uscita è composto da PET trasparente, colorato e azzurro, HDPE, PP, PE+PP, LDPE+PP, plastiche ingombranti (quattro prodotti diversi), residui, residui fini, metalli non ferrosi e metalli ferrosi.
L’impianto di Parma è progettato per trattare i flussi di materiale proveniente dalla raccolta differenziata di carta e plastica e si basa su due linee di selezione estremamente integrate che consentono di ottimizzare gli spazi, condividendo il sistema di pressatura. In particolare, la linea di selezione della plastica, con una capacità di nove tonnellate all’ora, tratta bottiglie in PET+HDPE+PP, film in PE+PP, plastiche ingombranti, imballaggi in plastica mista, metalli non ferrosi e metalli ferrosi mentre la linea di selezione della carta, con una capacità di 20 tonnellate all’ora, processa cartone e carta mista ed esegue il processo di de-inchiostrazione. Ogni linea è composta da una sezione di alimentazione, una per la selezione meccanica e ottica, una cabina di cernita per la selezione manuale dei rifiuti ingombranti e una sezione di stoccaggio e pressatura. Nella linea di selezione della plastica, in particolare, una volta rimossi i rifiuti ingombranti all’interno della cabina di pre-cernita, i rifiuti industriali possono essere inviati a un trituratore. In seguito, un grande vaglio a tamburo rotante effettua la prima selezione in base alle dimensioni del materiale. La frazione ingombrante è inviata direttamente alla cabina di cernita, dove gli operatori la suddividono in tre diversi prodotti. Il flusso di materiale principale di medie dimensioni (50-380 mm) viene alimentato a un separatore balistico STT5000, che divide i prodotti secondo le loro caratteristiche balistiche e di peso in frazione fine, 3D (oggetti pesanti e/o rotolanti) e 2D (oggetti piatti e leggeri). Tutte le frazioni passano quindi attraverso l'impianto composto da: tre separatori ottici per differenziare i diversi tipi di plastica; un sistema di separazione ad aria per migliorare la separazione 2D e 3D; un separatore magnetico in grado di separare i metalli ferrosi; un separatore a correnti parassite per la segregazione dei metalli non ferrosi.