Rotational moulding becomes smart
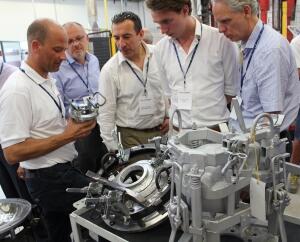
Smart is the name of the new range of rotational moulding plants by Persico. The news was announced on 18 June during the presentation of the results of the Rotofast project, which saw the involvement of the company based in Nembro (near Bergamo, Italy), along with various Italian and European partners. The first Smart machine will be ready at the end of August or early in September, and the official launch will take place at K 2013 (Düsseldorf 16-23 October). The range was developed by combining conventional rotational technology with the Leonardo system, also developed by Persico, with the goal of expanding the market potential for rotational moulding, broadening the array of special materials that can be processed.
The machines are similar to the traditional single-arm moulding machines, while the aluminium moulds, which are processed on a CNC machine, have a thickness of 5 to 10 mm and are provided with special grooves to accommodate the electrical resistances used to heat them. The moulds are fitted with temperature sensors, internal cooling devices and all the features required by the Leonardo system for process control. In addition, they can be equipped with automatic opening and closing devices and have 16 heating zones to reach a maximum power of 100 kW. The quick mould change prevents machine downtimes during this operation. The Leonardo system for automatically controlling the moulding cycle is based on the temperature of the air inside the mould and the production cycle is monitored by a PLC in which all the parameters have been preset.
Electrical heating makes a heating and cooling unit superfluous, reducing the overall weight of the mould, lowering energy consumption without imposing temperature limits to the process while increasing heating efficiency. In terms of performance, it is possible to reach a peak temperature of 350°C and heating is more uniform, to the order of ±5°C, with optimal distribution throughout the thickness of the mould. In addition, the heating cycle is more rapid, with a temperature increase from 70°C to 220°C in approximately 4 minutes. Even cooling, effected by localized fans or Venturi devices, is more uniform, preventing the eventual warping of the manufactured part, and it is also faster, going from 220°C to 70°C in about 7 minutes, and can be even interrupted at specific temperature values.
The plant has a compact and flexible layout and can be equipped with optional internal pressure control unit and vacuum device. The process is efficient, repeatable and fast. Potential fields of application include the production of technical articles with strict tolerances and complex geometries, aesthetic parts and the co-moulding of metal inserts.