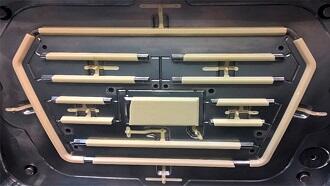
Con la tecnologia FLEXflow, lo specialista italiano nella costruzione di canali caldi HRSflow ha sviluppato una soluzione innovativa per lo stampaggio a iniezione di componenti di alta qualità destinati principalmente all'industria automobilistica. FLEXflow è un sistema di otturazione servocontrollata con regolazione di precisione per sistemi a canale caldo. Il controllo preciso del flusso del fuso attraverso ogni singolo ugello del canale caldo permette un riempimento estremamente equilibrato di tutte le impronte e una distribuzione uniforme della pressione durante la fase di compressione, anche in presenza di più punti di entrata e di impronte molto diverse.
La griglia per radiatore prodotta con uno stampo per test da 580 x 330 mm equipaggiato con HRSflow, con peso totale delle parti di 297 g e spessore pareti variabile da 2 a 3 mm, viene successivamente sottoposta a cromatura e, pertanto, deve soddisfare requisiti molto stringenti in termini di qualità superficiale. Diversi fornitori di componenti auto hanno già testato con esito positivo questa griglia in ABS e ABS/PC sulle loro apparecchiature di cromatura elettrolitica. Le prime applicazioni commerciali di cromatura andranno in produzione di serie prossimamente.
Pesi di stampata diversi e un unico processo di riempimento
Grazie al sistema di otturazione FLEXflow è possibile stampare parti ancora più grandi garantendo un’elevata qualità superficiale. Con il processo di stampaggio a iniezione a cascata utilizzato normalmente a questo scopo, l’otturatore ad azionamento elettrico assicura una precisa apertura e chiusura sequenziale dei perni a velocità variabile per l’intera lunghezza della corsa. Ciò per converso consente un controllo preciso in generale sia del flusso del fuso su ciascun punto di entrata caldo sia del volume di flusso nell’impronta. Con l’apertura personalizzata dell’otturatore, è possibile evitare le spiacevoli perdite di pressione che si verificano con i metodi di stampaggio a cascata convenzionali, e di conseguenza anche i segni causati sul manufatto. Inoltre la posizione controllata del perno in fase di compressione consente di ottenere un controllo indipendente della pressione su ciascun punto di entrata e quindi del ritiro previsto per ciascuna impronta, accelerando il raggiungimento dei requisiti di tolleranza ed evitando costose modifiche agli stampi.
La griglia per radiatore è prodotta con un’unica stampata con dieci punti di iniezione dotati di ugelli HRSflow serie MA. Il layout del sistema consiste in un canale compatto asimmetrico. Il volume delle impronte per le singole parti della griglia presenta un rapporto di 1:20 dall’impronta più piccola a quella più grande, e una differenza di spessore di parete del 30% tra quello minore e quello maggiore. Il tempo di iniezione è pari a 2,9 secondi, il tempo di mantenimento a 6 secondi, la temperatura del canale caldo raggiunge i 255°C e la temperatura dello stampo i 60°C.
In passato, per ottenere i diversi pesi di stampata e mantenere nel contempo i requisiti di tolleranza per la cromatura e l’assemblaggio, si doveva ricorrere a più stampi per la produzione di parti di qualità. L’obiettivo di questo sistema a canale caldo di HRSflow era quello di testare i punti di forza della tecnologia FLEXflow in un’applicazione multiimpronta. Nicola Pavan, coordinatore dell’ufficio CAE e project leader presso HRSflow commenta al proposito: "Per testare le capacità di FLEXflow abbiamo voluto stampare i componenti solo con l’apertura simultanea degli ugelli a otturatore ad azionamento elettrico con una regolazione predefinita della corsa di apertura. Il volume del fuso iniettato per ciascun singolo ugello viene controllato con precisione nel corso delle fasi di riempimento stampo e compressione variando le corse degli otturatori fino a ottenere la pressione locale desiderata. In questo modo abbiamo un controllo localizzato dei flussi e delle pressioni applicate e la possibilità di bilanciare facilmente gli stampi famiglia e controllare l’imbarcamento senza modifiche alle parti o al canale”.
Analisi di simulazione con Moldex 3D
Un’analisi del riempimento dello stampo con i due programmi di simulazione Moldex 3D e Autodesk Moldflow è servita per calcolare i parametri ottimali per ciascuno dei 10 ugelli del sistema FLEXflow. Nel corso della fase di iniezione, ciascun otturatore assume una posizione liberamente programmabile da parte dell’utilizzatore. Gli otturatori possono essere programmati per un numero massimo di 8 punti di controllo sia in apertura che in chiusura, definendo velocità e posizione per singolo punto. Per ciascun otturatore è possibile programmare fino a due cicli di apertura e di chiusura. L’analisi di simulazione e la pratica applicativa dimostrano un’elevata conformità con l’avanzamento reale del fronte del flusso nelle singole impronte.
"FLEXflow riequilibra i diversi pesi di stampata in maniera ottimale e riempie i volumi delle impronte di ciascuna parte in contemporanea, evitando quindi problemi come le bave, riducendo l’imbarcamento e consentendo un controllo preciso delle linee di giunzione" sintetizza Nicola Pavan. Grazie alla tecnologia FLEXflow diventa possibile, con un tempo minimo di regolazione, produrre parti prive di difetti superficiali malgrado i limiti tipici degli stampi famiglia. Ciò consente a sua volta al trasformatore di ridurre la quota di pezzi difettosi. Le parti stampate inoltre evidenziano minori tensioni di raffreddamento, nessun fenomeno di impaccamento, un imbarcamento controllato e si adattano in maniera ideale al processo di cromatura.
Parti di migliore qualità
Con FLEXflow, gli otturatori dei 16 ugelli del canale caldo possono essere individualmente aperti e chiusi in sequenza in maniera precisa e indipendentemente l’uno dall’altro. A seconda della fase (apertura o chiusura) è possibile predefinire fino a 8 posizioni per l’otturatore con una tolleranza di azionamento di ±10 micron. Grazie a questa estrema precisione del posizionamento e del controllo della velocità dei perni degli otturatori, diventa possibile ottenere una distribuzione molto omogenea della pressione all’interno dell’impronta e quindi nell’intero processo di stampaggio. Come conseguenza del notevole ampliamento della finestra di processo, è possibile ridurre la forza di chiusura dello stampo e perfino il peso delle parti senza produrre alcun effetto negativo sulla qualità. Nelle costruzioni automobilistiche, la tecnologia FLEXflow assicura vantaggi in particolare nello stampaggio a iniezioni di grandi parti per esterni ed interni come paraurti, spoiler, supporti per quadri strumenti (IPS), rivestimenti interni per porte, e per il tetto, componenti del sistema di illuminazione, cristalli, fanalerie e tetti panoramici.