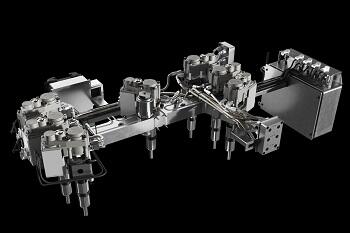
Quali sono le principali anomalie che si riscontrano durante il processo di iniezione e come individuarle? Se si prova a immaginare il componente stampato più complesso di sempre si deve considerarlo come il risultato di un delicato equilibrio tra la selezione del polimero, i corretti parametri di processo, l’accurata progettazione dello stampo e del componente stesso. I fattori che possono influenzare il processo di iniezione sono diversi, dalla pressa al materiale di stampaggio. Ma come individuarli? La giusta combinazione di tecnologie consente di evitare i difetti sulla parte stampata assicurando un risultato di qualità nel minor tempo possibile.
Una delle cause della variabilità di processo può essere legata per esempio alla pressa a iniezione. Se alcuni dei suoi componenti - quali vite, cilindro, anello di tenuta - mostrano segni di usura, il processo può variare in modo significativo. L’incostanza durante le fasi di iniezione, impaccamento o dosaggio possono infatti essere la causa alcuni difetti sulle parti stampate.
Un altro elemento che può influenzare il processo di iniezione è legato invece alle variazioni di viscosità del materiale di stampaggio. È stato osservato che lotti differenti di materiale plastico possono comportarsi diversamente durante il processo. Inoltre, l’eventuale utilizzo di una percentuale di materiale riciclato può essere una delle cause di variabilità del processo.
Dunque, queste problematiche come possono essere rilevate per evitare la deriva del processo? Grazie ai sensori di pressione è possibile avere un feedback diretto della costanza del processo monitorando lo stato reale del polimero in cavità. Inoltre, è possibile rilevare la presenza di cicli anomali evidenziando quali di questi vanno fuori tolleranza. Grazie ai sensori di pressione si può definire se vi sono derive progressive, ovvero più cicli che progressivamente si allontanano dall’ideale.
L’utilizzo dei sensori di pressione nello stampo consente ai sistemi a canale caldo a otturazione di essere comandati da condizioni verificate all’interno dello stampo/cavità e non sulla base di comandi esterni agli stessi, quali posizione della vite o tempo. Questo permette al processo di adattarsi alle situazioni reali.
La combinazione tra i sensori di pressione e Flexflow Evo - il sistema a otturazione servo controllata sviluppato da HRSflow - consente di avere un controllo preciso di tutto il processo di iniezione rilevando così le problematiche relative al materiale di stampaggio o alla pressa.
La tecnologia elettrica è progettata per controllare in maniera indipendente ciascun otturatore, aggiustandone con precisione posizione e forza, in fase sia di apertura che di chiusura. Questa soluzione garantisce un controllo accurato e flessibile della pressione e del flusso di materiale durante l’intero processo di stampaggio minimizzando la variabilità e consentendo una flessibilità di design di gran lunga superiore.
I sensori di pressione insieme al sistema Flexflow Evo consentono di evidenziare lo stato del polimero in cavità dello stampo ritardando o anticipando la fase di apertura o chiusura. Questa combinazione assicura non solo la massima affidabilità e ripetibilità del processo ma anche una qualità uniforme dei pezzi stampati con il minimo scarto possibile.