Productivity and economic efficiency in PET recycling
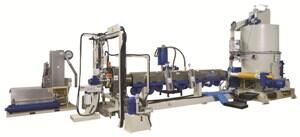
The PET recycling lines belonging to the new GM Compac series, developed by Gamma Meccanica, are equipped with an Ecotronic system, extruder, screen changer, and TI underwater die-face cutter, and guarantee high energy efficiency, high productivity, and uniform, defect-free granules. By means of the Ecotronic device, the Compac feeder prepares the material for the subsequent stages in the recycling process. The material is first shredded by rotating blades and then densified, with much of the moisture being allowed to evaporate. The Ecotronic device guarantees low energy consumption while the extruder, to ensure total expulsion of any residual moisture, is equipped with a degassing station and a forced vacuum system. Furthermore, the extruder is fitted with a screen changer specifically for the processing of PET. The TI underwater die-face cutter, designed to treat all the main polymers on the market, is ideal of the processing of highly flowable materials, such as PET, of course, hot-melt, TPU, PA, and so on.
In order to enhance the performance of the line, make it easier to use, and speed up its maintenance operations, certain improvements have been made compared with the company's previous models for this type of application. For example, the new series features sealing gaskets on the drive shaft and allows monitoring of the status of the heaters and opening of the cutting chamber to allow rotating blade replacement. The centrifuge has been equipped with a new drive system, making it possible to operate at the speed most suitable for the type of material being recycled. Noise emissions generated by the passage of the granules have been significantly reduced. The hourly working capacity of the GM lines for PET, which yield a product that can be fed back directly into the production process, ranges from 150 kg (for the GM65 Compac, which is the smallest version) to 2200 kg (for the GM210 Compac).