Viscosities up to 50% lower than conventional TPV
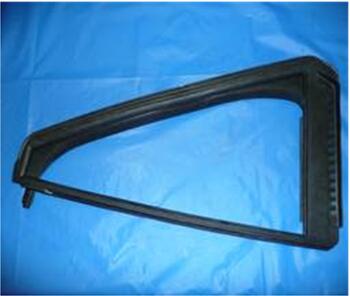
The new EZPrene SHF (Super High Flow) series of vulcanized thermoplastic elastomers (TPVs) has been introduced in Europe by Ravago Petrokimya and it is produced thanks to a company’s proprietary cure technology. It currently includes 3 grades, ranging in hardness from 65 to 90 Shore A. Each material has been developed to offer injection moulders higher melt flow rates, shorter fill times, longer flow paths, and lower injection pressures. And, like every product in the EZprene TPV family, they are non hygroscopic, so they require no pre-drying prior to processing.
“The viscosity levels exhibited by these materials are quite remarkable”, says Hamid Tavakoli, the company’s product manager on these materials in the United States. “The SHF grades flow so much better that injection moulding cycles can be as much as 15% shorter than with traditional vulcanized thermoplastic elastomers and EZPrene SHF TPVs are used for many years in the US”.
Initial evaluations moulded parts indicate that surface aesthetics attainable using EZPrene SHF TPV materials are superior to those achieved using conventional thermoplastic elastomers. “Gloss levels are controlled and consistent”, points out marketing manager Synco de Vogel, “and weld lines are much less apparent”.
Materials in the EZPrene SHF TPV series are very stable, and they can be processed at higher temperatures than standard TPVs. These products can be processed in a wide temperature window up to 250°C without showing signs of degradation. Processing at elevated temperatures accelerates and improves bonding to other TPVs in applications such as corner mouldings for automotive glazing.
Among the uses for which the TPV series was developed is the encapsulation of window glass, which typically involves lower temperatures (between 190°C and 245°C), and lower moulding pressures to avoid glass breakage. At such temperatures, the new EZPrene 65A-400B SHF material exhibit viscosities that remain 40 to 60% below those of traditional TPVs, which can contribute to lower scrap rates and lower costs.
In soft-touch or flexible injection moulded parts, the new EZPrene SHF materials are ideal for hard-to fill moulds, such as parts with very thin walls or those involving long or complex flow paths. The excellent surface aesthetics produced by these elastomers is particularly important to designers of automotive interiors. An extensive body of weathering data has shown these materials to be UV stable in use. In addition, these products exhibit chemical resistance, oil resistance, and compression set comparable to thermoset rubber.
Because the cure technology common to all EZPrene TPV materials results in a clean, consistent natural, the new SHF materials can be easily produced in black or in a wide range of colours, including the lightest pastels.