Piggyback extruder saves space and energy
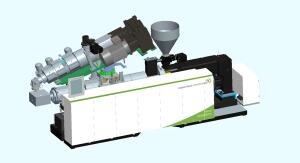
At the K 2013, battenfeld-cincinnati will underscore the significance of the VDMA's BlueCompetence initiative, in which the company is involved as a partner. The company will present extrusion solutions which operate energy-efficiently, save material and consequently offer their respective industries the best possible cost/benefit value.
This year's highlight is the piggyback extruder solution consisting of a parallel twinEX 78-34 P and a conical conEX 63 P extruder. With this compact machine configuration, the machine manufacturer caters to the growing trend towards using more recycled materials in the window profile industry. For both ecological and economic reasons, up to 40% regrind is used today in window main profile production in non-visible areas. The machine combination on display is laid out for a throughput of up to 500 kg/h. Like all extruders from battenfeld-cincinnati, both extruders are equipped with energy-efficient AC motors, Intracool screw core tempering and fully insulated barrels with intelligent air cooling. The piggyback solution is the answer to the BlueCompetence demand for material savings.
At the same time, the extruder combination is extremely user-friendly for connecting extrusion dies, thanks to the coextruder's flexible frame design. The equipment's user-friendliness is further enhanced by a common control cabinet, one control unit serving both extruders, and a central plug, by which the die can be connected quickly and easily and without the risk of errors.