High temperature process for fluoropolymers
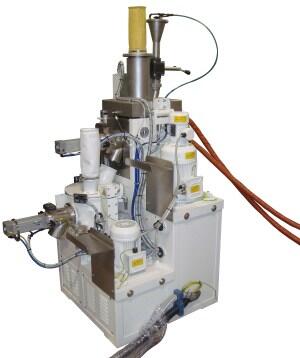
The Plasmec High Temperature Bonding System (HTBS) project is the result of a request, by a leading company in the industrial surface treatments industry that specialises in the creation of non-stick and anti-wear coatings, to develop a small-scale plant capable of creating a special bonding cycle to produce a new type of fluoropolymer perfected in their own research and development laboratories. The bonding process is the process of adhesion of the pigment (metal) to the base, in such a way as to prevent their separation during application and recovery of product in the cabin of application.
During the initial project development phase, engineers concentrated on how to achieve heating of the material to the process temperature. To do this, they opted for a mixing tank with a cavity into which diathermic oil, heated in an external heat regulation unit specially designed by one of Plasmec technical partners, is made to flow. To control the temperature of the fluid it was decided to implement a PID controller, and this allowed optimum management of this important process parameter. The need for working at high temperatures meant it was necessary to completely redesign the transmission and mechanical seal units. The development of these components was carried out with the aid of the most up-to-date design tools (3D Cad, FEM and CFD) so that they could be assessed, even at the design stage. The problems of thermal insulation of the machines and thermal dilation were dealt with using the same methods.
As regards insulation, the aim was to reduce heat loss to a minimum and bring the potential contact surfaces up to the values foreseen by the standards. Here again, careful calculations and numerical analysis were carried out in order to select the right insulating material (ceramic spacer components and ceramic-silica fabric) for the mixer and the pipes connecting it to the heat regulation unit. Also, thanks to the analysis of thermal simulations it was possible to avoid problems relating to thermal dilation by identifying critical areas that required careful design and by making wide use of ceramic-based materials.
As regards problems with mixing and the volatility of the compound, careful design of the individual stages in the mixing equipment, the mixing tank cover, an innovative system of fluxed seals and a type of filter element, specifically designed for this application, have enabled to keep the material within the volume of operation of the blades, even at high mixing speeds. This gave undoubted advantages for dispersion and homogenisation of the various components in the mix, as shown by the laboratory tests performed by the client.
The need for high process temperatures contrasted with the need to safeguard against the risk of explosion, as was brought to light in the initial risk analysis. To deal with this, a series of countermeasures were adopted at design level to eliminate all possible trigger sources, in particular within the mixing tank (accumulation of static electricity, uncontrolled temperature increases in mechanical parts, sparks caused by rubbing of moving components). Externally, much work went into the selection of suitable components for Atex 22 classified environments and on the creation of the area around the machine. The risk analysis carried out following these modifications did not show any particular residual risks, and by following the requirements of the Atex standard it was possible to declare the machine compliant with CE EX II 2/3D IIIC T135°C.
The need for flexibility, required to use the plant to carry out tests on new formulations, was satisfied by working both at mechanical configuration and at control system level. Mechanically speaking, work was carried out to allow rapid changing of the mixing tool configuration, also providing various types of interchangeable blade. As regards the control system, while maintaining the levels of automation typical of production plants, an attempt was made to make it as complete as possible by implementing a whole series of typical laboratory functions that will allow technicians to create the recipes to be processed in a fast, intuitive manner.
In order to satisfy the cleaning requirements, the mixer and the cooler were equipped with easy-to-reach discharge outlets that can be completely dismantled for fast cleaning. The mixing tool itself can be dismantled using a single tool, while the entire mechanical and pneumatic section is protected by removable guards to reduce deposits of environmental dust on the components to a minimum.