Flame treatment system for improving receptivity to ink
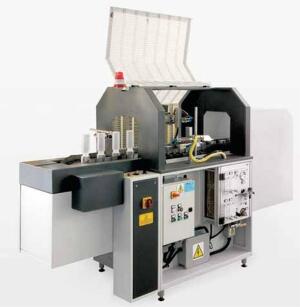
For the high-speed flame treatment of items which cannot be pre-treated on board the process machine, Tosh is offering the FT100/2 belt flame treatment system. Flame treatment is used to increase the wettability of certain plastics prior to printing, which makes them more receptive to ink. Such surface treatment is necessary for certain types of materials which would otherwise be impossible to decorate, because their physicochemical properties are incompatible with the ink.
Good adhesion of ink on the material to be decorated is achieved when the material has a surface tension - measured in dyne (mN) - greater than that of the ink itself. In the case of solvent-based inks, which are the ones most commonly used in pad printing, the surface tension of the material to be decorated must be at least 40 dyne/cm. Certain materials - such as PE and PP, which have a low surface tension - require a treatment that guarantees good adhesion of the ink. As well as increasing surface tension, flame treatment also removes any impurities that would prevent uniform adhesion between the ink and the surface, and can be used as a post-treatment on materials such as acrylic resins to anchor the ink. On the whole, flame treatment is the most widely used pre- and post-treatment method for three-dimensional objects in high hourly-throughput production lines.
The FT100/2 flame treatment system consists of a burner unit and a belt conveyor for transporting the parts. The flame treatment unit comprises a generator of the (compressed) air and gas (propane, butane, or methane) mixture, an electrical panel, a junction box controlling the gas-air-flame detector solenoid valve, and a junction box controlling the piezoelectric transformers for igniting the flame. All the flame regulation parameters can be managed and viewed from the PLC. In addition, there are two type MPR3/100 burners, mounted opposite each other on the conveyor belt frame, with the ability to separately adjust the pre-treatment position. Finally, there is a guard with double (left/right) openings, that can be separately opened to access the burners and make adjustments.
The conveyor system is equipped with a galvanized pressed-steel slat conveyor with a thickness of 4 mm, pitch of 63.5 mm, width of 210 mm, length of 1850 mm, capacity of 3-4 kg/m and adjustable speed from 0.12 to 0.80 m/minute. The parts to be treated are aligned by a telescoping guide mounted on one side at the start of the conveyor, while a double V-guide is used to straighten the parts immediately prior to treatment. Detection of the presence of the part to be treated, and the corresponding signal to activate the burner, with height and depth adjustments, are accomplished by a photoelectric sensor.