Festo wins the Arburg Energy Efficiency Award
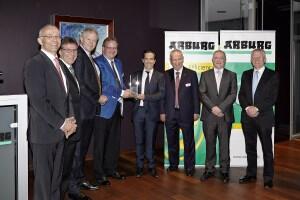
Since 2008, Arburg bestows this award each year to a company for outstanding activities in the field of energy efficiency. Officially presented on March 18, the winner for 2014 is Festo, global supplier of technology for automation. The company has won the award for the conception of its new plastic parts production facility, which is fully geared towards energy efficiency, as well as cooperation on the Freeformer, the new Arburg 3D printing machine.
"The intensive business relations between Festo and Arburg have grown over 30 years, with both family-run companies exchanging know-how that goes far beyond the product level. This happened both with regard to Festo's new plant in Hassel/St. Ingbert in Germany and to the Freeformer, which expanded the Arburg product portfolio in 2013 to include additive manufacturing. Both of these examples make important contributions to the future-oriented enhancement of energy and production efficiency and were therefore decisive for presentation of the Arburg Energy Efficiency Award 2014 to Festo", said Herbert Kraibühler, managing director technology and engineering.
"Since many years, we invest in energy efficiency. It's encouraging that our efforts and investments are recognised, which lends credence to the course we have embarked on. Together with Arburg, we have taken a consistent approach in examining energy flows, asking new questions, finding new solutions and adopting new approaches", explained Claus Jessen, director product supply at Festo. He also added that Festo had identified plastics technology as a key technology for the global competitiveness of its products several years ago and had decided to develop top-class expertise in this area.
Festo decided to set up a plant with a completely new polymer production facility and a focus on energy efficiency, the Global Production Centre Hassel, at its St. Ingbert location in the Saarland. The plant is currently under construction and will be finished in early 2015. All the important factors in terms of the building, production and machines are taken into account there. Thanks to its many years of know-how in this sector and its holistic approach, Arburg was an important advisor and partner for Festo in this area.
The two companies jointly examined the 45 Allrounders for thermoplastic and 12 vertical Allrounders for elastomer processing in detail with regard to energy requirements and production efficiency. Arburg was then tasked with devising optimal machine concepts. For the thermoplastics, electric Allrounder Alldrive machines were selected, which were specially configured to meet the requirements at the Hassel plant. For the elastomers, the machines are to be converted to speed-regulated pump drives.
The key elements of the holistic concept also include insulation of moulds and plasticising cylinders, optimisation of material pre-drying and supply through an efficient central solution and waste reduction, e.g. through lower sprue weights and fewer hot runner connections. Due to the nature of the products, the temperature levels were selected so that cooling is only necessary during midsummer, meaning that heat recovery can be dispensed with.
Festo was already supplied with a Freeformer in early 2013 in order to subject it to in-depth testing from a user point-of-view. The Freeformer expands the energy and efficiency end of the Arburg portfolio because fully functional one-off parts and small-volume batches can be produced very cost efficiently directly from standard granulates without a mould using 3D CAD files. The results and feedback from Festo provided Arburg with valuable information for optimisation and further development. Festo sees opportunities for using the Freeformer in its own business predominantly in the areas of prototyping and, following subsequent further development, in small-volume production.