Awards to originality, creativity and technical ability
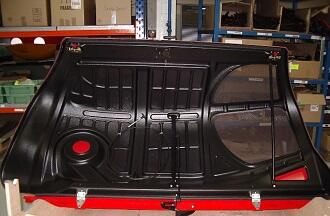
In 2006 the European Thermoforming Division of the Society of Plastics Engineers sought the first time to initiate an independent, sector-oriented award, the European Thermoforming Parts competition. This award stands for first-class innovative achievements in originality, creativity, mould complexity and technical ability in order to promote advanced design and developments of thermoformed applications.
For the sixth time, in 2016 the European Thermoforming Parts Award once again highlighted applications, selected by the jury at the recent European Thermoforming Conference in Sitges (Spain) from March 9 to 11, 2016.
The awards winners were the following
First prize winner for heavy gauge - vehicle/automotive applications
Part: “Engine Hood” + 50 components integrated in a plug and play function, produced by Technoplast Industries, France.
Material type: ABS PMMA + PA6 15% GF
Unique
qualities: 150°C (170°C peak) high resistance to chemicals/fluids because of double
skin in PA6 + 15% GF
Jury´s motivation: “A large area cosmetic forming but for an industrial application. Surface finish is good. Well formed and trimmed - both parts are well assembled, good integrity in bonding and highly functional part”.
First prize winner for heavy gauge - building applications
Part: “Velux” roof dome produced by Formplast, Sweden
Material type: PC UV
Unique qualities: the high optical quality on the thermoformed part. To reach the very high demand of optical clarity by use of normal positive thermoforming is very difficult.
Jury´s
motivation: “Excellent clarity using a fairly complex sheet material which
requires a great deal of preparation. Good industrial application - high risk
product”.
First prize winner for thin gauge - food packaging applications
Part: “Veggiefresh” IML-T tubs and lids with premium decoration qualities, produced by RPC Bebo Plastik, Germany
Material type: PP
Unique qualities: wide label coverage of body including stacking rim, barrier options through multilayer sheet for oxygen and UV barrier, as well as light protection, utilization of existing tools
Jury´s motivation: “The way to beat injection moulding, nice volume thermoformed IML to the product”.
First prize winner for thin gauge - vehicle/automotive applications
Part: “Back
lighted day-night effect baguette” produced by WalterPack, Spain
Material type: PC with multi-layer of inks
Unique qualities: a 10 layer printed foil, high pressure formed at 100 Bar, UV cured and back injected part to obtain a decorative back lighted baguette for automotive applications with a day-nigh effect
Jury´s motivation: ”Advance high pressure forming - superbly done”.