Manifattura additiva di componenti di volo pronti all’uso
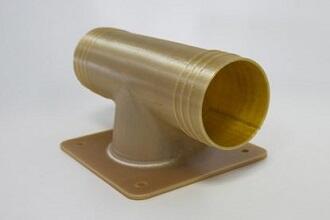
La tecnologia per la stampa 3D di Statasys è stata scelta da Marshal Aerospace and Defence (una delle aziende aerospaziali private più grandi al mondo) per stampare componenti pronti all’uso e realizzare specifiche attrezzature di terra per un programma di costruzione di nuovi velivoli militari, civili e di trasporto. La stampa 3D consente all’azienda di produrre in modo più rapido ed economico componenti approvati per il volo più leggeri rispetto a quelli realizzati con i metodi tradizionali.
Secondo Chris Botting, ingegnere addetto ai materiali, ai processi e alla fabbricazione additiva di Marshall, la capacità di realizzare componenti precisi, ripetibili e affidabili mediante la stampa 3D di materiali avanzati approvati per il settore aerospaziale è il fattore chiave per ottenere i requisiti necessari in termini di prestazioni per le applicazioni di volo.
"Nei programmi complessi di ingegneria abbiamo bisogno di un metodo in grado di realizzare un condotto preciso, complesso, funzionale e leggero in modo efficiente e con costi di attrezzaggio minimi. È qui che si inserisce perfettamente la stampa 3D. Ma abbiamo anche bisogno di garantire che il condotto prodotto sia approvato per il volo dall'EASA. Di conseguenza, stiamo utilizzando la stampante FDM Fortus 450mc e la resina Ultem 9085, un materiale per la stampa 3D resistente e allo stesso tempo leggero, caratterizzato da un'elevata resistenza termica e chimica. Questa scelta si è rivelata fondamentale per rispettare i rigidi requisiti del settore, dal momento che ora possiamo stampare in 3D parti con i requisiti di fiamma, fumo e tossicità desiderati da utilizzare all'interno del velivolo", ha spiegato Botting.
Marshal, inoltre, utilizza la stampante Fortus 450mc per realizzare componenti da utilizzare a terra. Di recente, l’azienda ha creato il prototipo di un adattatore per i condotti delle attrezzature con cui fornire l’aria per raffreddare l'avionica del velivolo. La stampa 3D di questo componente ha consentito a Marshall di abbandonare i costosi processi basati su attrezzature in alluminio.
"Prima di impegnarci nella lavorazione a macchina dell'alluminio, un processo particolarmente costoso, abbiamo utilizzato la Fortus 450mc per stampare in 3D un prototipo in ASA. In questo modo siamo riusciti a creare un prototipo funzionale preciso di un componente complesso. Successivamente, abbiamo dimostrato la possibilità di stamparlo in 3D utilizzando il PA 12 invece del metodo più convenzionale della lavorazione a macchina partendo dall'alluminio. Il condotto stampato in 3D ha consentito una riduzione notevole dei costi rispetto alla lavorazione a macchina della parte a partire dall'alluminio, oltre a una riduzione del 63% del peso complessivo", ha aggiunto Botting.
Marshal sta utilizzando le stampanti 3D di Stratasys anche per realizzare una gamma di attrezzaggi complessi, incluse guide di foratura, modelli di maschere, staffaggi congiunti e attrezzaggi compositi realizzati con l'ausilio di stampi. L’azienda realizza regolarmente lotti ridotti di strumenti personalizzati in sole 24 ore dalla richiesta del reparto tecnico. Viene quindi promosso l'uso di strumenti in materiali termoplastici stampati in 3D per sostituire strumenti pesanti in metallo, diminuendo il carico sull'operatore e riducendo notevolmente il costo e i tempi di lavorazione per le attività operative urgenti.
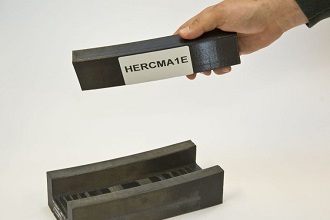