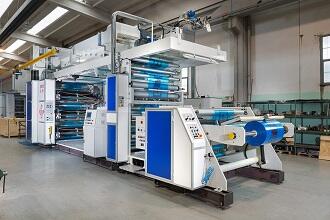
In the plastic sector since 1975, BFM is today one of the main Italian manufacturers of automatic bag-making and flexo-printing machines, both with “CI” central drum, up to 10 colours, or stack type, up to 8 colours, reel-to-reel or in line with the extrusion and/or bag-making machines. For the company, it is important and decisive the partnership with Bandera, one of the main global manufacturers of extrusion lines, for which BFM realizes rotating take-offs and automatic winders.
New flexo-printing machine
In recent years, BFM’s machines have all undergone important technological upgrades and, at K 2016, in Düsseldorf, the new Sirio flexo-printing machine was introduced.
It is a 6-colour stack type printing machine, designed for a wide range of plastic materials but suitable for some paper materials as well. The machine can be used in line with the extruder or in reel-to-reel mode.
The printing groups, placed horizontally, are provided with closed chamber, “doctor blade”, with self-alignment option. The printing length ranges from 300 to 1,200 mm with widths of 800, 1,000, 1,200, 1,400, and 1,600 mm; by changing the web paths, it is possible to print both sides: 6+0, 5+1, 4+2, 3+3.
The unwinding unit is provided with hydraulic loader for reels and motorized tension control. Each printing group is equipped with motorized printing cylinder, electrical ink grinding, and pneumatic inking. The drying system includes both intercolour fans and drying tunnel, with electrical or gas heating. The nip roll section features an independent motor and chilled rollers. The winder is motorized and provided with hydraulic unloader for reels.
The machine transmission and automation have been designed with the support of Bosch Rexroth, in order to optimize mechanical sizing, to keep construction simple, and to speed up production changes.
All printing groups, as well as the unwinder/rewinder unit, are equipped with MBT torque motors from Bosch Rexroth, which can work with high torque and reduced ripple. This has resulted in significant kinematic reduction, leading to cost efficiency, improved performances, easier maintenance and, above all, higher printing precision, thanks to the IndraDrive digital drives.
Bag making machines
As for
bag-making machines, a new line was also introduced for the production of “sac-a-poches”
(on roll), triangular-shaped very elastic pastry bags made by a special 3-layer
coextruded material, with thickness from 90 to 100 micron.
The production process starts with a tubular reel. After a double nip-roll to control the tension of the reel, a station for inclined precutting and sealing is placed on the accessory section of the machine and a transversal cold precutting unit is installed in the main machine section. The collection of the sac-a-poches is carried out by a mini-roll device, winding up the 100-200 bag rolls. Finally, the rolls are placed in a conveyor belt. The production output is approximately of 100 bags per minute.
Apart from the BM180 base model, also used for other applications (e.g. soft handle bags, patch handle bags, etc.), all accessories have been designed according to customers’ requirements.