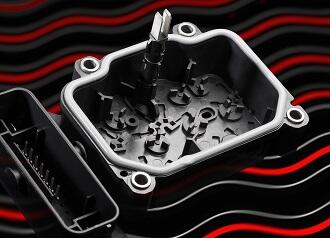
The demand of the automotive industry for highly effective sensors for the expansion of electric mobility and autonomous driving is increasing. So Basf has further developed its range of hydrolysis-resistant thermoplastic polyesters. The expanded range of Ultradur HR (Hydrolysis Resistant) comprises Ultradur B4330 G6 HR High Speed, a particularly flowable and laser markable grade with 30% glassfibre reinforcement, Ultradur B4330 G10 HR, a highly reinforced grade with 50% glass fibres as well as Ultradur B4331 G6 HR, the next generation with optimized processing characteristics. Ultradur B4331 G6 HR is available from now on as uncoloured grade, in a black laser markable version, and in orange for components in electric cars.
With its Ultradur HR grades, Basf offers highly resistant PBT materials which are especially suitable for use in challenging environments. They thus enable a long service life and an excellent operational reliability of automotive components. The HR grades also have a considerably increased resistance to alkaline media which trigger stress corrosion cracking. This is also true of the new Ultradur B4331 G6 HR grade with considerably improved melt stability and flowability. In tests, Ultradur B4331 G6 HR does not display any increase in viscosity even with long residence times and at high temperatures – the best basis for stable and easy processing. The material can also be coloured in orange (RAL 2003) in order to produce high-voltage plug-in connectors for electric cars. Thanks to the unusually high tracking resistance for PBT, the plug-in connectors can be designed smaller and still withstand the higher voltages in electric vehicles. Thus savings on costs and component weight are possible.
The Ultradur 4330 G6 HR series which is already available with 30% glass-fibre reinforcement has been expanded to include the particularly flowable and lasermarkable
Ultradur B4330 G6 HR High Speed bk15045. With this grade, thin-walled parts and components which show a high ratio of flow path to wall thickness can easily be produced.
The new Ultradur B4330 G10 HR is filled with 50% glass fibres. It can therefore be processed to components which are simultaneously exposed to moisture and high temperatures (160°C, short term up to 180°C) and keep a high stiffness, e.g. steering modules in the charge air duct. In the temperature range from 140°C to 180°C, the material reaches almost the property level of polyphenylene sulphide (PPS), which is usually employed in this kind of applications.
For selected automotive applications Basf has developed Ultradur B4450 G5 HR.
The PBT is reinforced with 25% glass fibers, RoHS-compliant and flame retardant.
It can be coloured in light colours and laser-printed. With its low fogging values according to the VDA 278 emission test, it is suitable for applications in car interiors and also for housings of control units. The newly developed material combines hydrolysis resistance with flame retardancy, high tracking resistance and low smoke density. This property profile is also aimed at electric vehicles with their considerable safety requirements and much higher currents than in conventional drive trains.
Since the market launch, Basf has developed around a dozen HR-modified Ultradur grades, with 15%, 30% and 50% glass-fibre reinforcement, particularly flowable, impact-modified, laser markable, laser transparent or flame-retardant. Typical applications can be found primarily in automotive electronics, e.g. housings of control units, connectors, sensors, but also charging plugs, housings of battery stacks or connectors in the high-voltage circuit of electric cars.