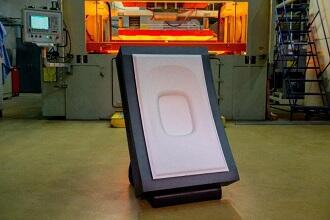
Among its exhibit highlights at Formnext 2018 (Frankfurt, November 13-16), Sabic is featuring its newest filaments for fused deposition modelling, including a tough filament made from its high impact EXL resin. Addressing industry needs for greater choice, Sabic is also demonstrating the use of its filaments in open architecture printers from a range of equipment manufacturers. Another focus area at the show is large format additive manufacturing (LFAM): Sabic is highlighting various tooling applications, as well as parts printed from its LNP Thermocomp AM portfolio of specialty compounds. The company is also highlighting recent breakthroughs in the use of its amorphous resins with standard selective laser sintering (SLS) equipment to provide a range of sinterable materials that extends beyond currently available semi-crystalline powders.
Differentiated resin capabilities, a broad portfolio and deep expertise empower Sabic to offer material solutions such as high heat Ultem resins, specialty copolymers and reinforced compounds to customers throughout the additive manufacturing value chain. Additionally, Sabic is able to provide materials in printable form when this brings value to the industry.
For example, at Formnext, the company is highlighting its award-winning EXL AMHI240F filament, a high impact material now available in white, as well as black. Its formulation, which includes a proprietary composition coupled with optimized colorant technology, provides up to four times the impact strength of standard polycarbonate (PC) and a more ductile failure mode in printed parts, as confirmed by Sabic’s material performance validation partner, RP+M. Sabic is showing several printed parts that demonstrate the versatility of EXL AMHI240F filament.
Sabic is involved in the research and development of new materials to help address the evolving needs of the industry. Featured at the stand are several developmental solutions that can provide improved performance versus options currently available in the market today. Sabic’s FST filament offers ease of processing along with low smoke and toxicity properties, and is capable of meeting OSU 55/55 requirements for aerospace applications. A second concept material featured at the stand is Extem filament for potential applications requiring higher-temperature performance than Ultem filament. Sabic is also developing an advanced breakaway support material to complement its aerospace grade Ultem AM9085F filament. The new support filament offers faster removal of the scaffold structure from parts with complex geometries, and can help reduce the cost of post-processing operations.
Also on display are several parts printed with Sabic’s high-performance filaments on a variety of open architecture printers, offering customers greater choice and the opportunity to pursue new application areas.
Sabic’s
portfolio of Thermocomp AM reinforced compounds, which includes materials based
on Ultem resin, is helping to encourage the use of LFAM for specialized
applications, such as high-temperature autoclave tooling for the aerospace
industry, reusable tooling for the cast concrete industry and a wide range of
lower-temperature large part thermoforming tooling. Printed tools can help to
reduce cost, construction time, inventory and weight vs. traditional steel
tools. Sabic is featuring a thermoforming tool for an aircraft interior panel
printed on a Thermwood LSAM machine using Thermocomp AM EC004XXAR1 compound, a
Sabic material based on Ultem resin with 20 percent carbon fibre reinforcement.
In addition to its development of tooling applications, Sabic is working closely with LM Industries Group, parent company of Local Motors, to validate various large format materials for printing finished components of its next iteration of Olli, the world’s first co-created, self-driving electric shuttle. On display in the stand is a fender from Olli, printed on a BAAM machine from Cincinnati Inc. using one of Sabic’s Thermocomp AM compounds.
To expand the scope of SLS, Sabic is developing innovative technology to help overcome some of the traditional drawbacks of amorphous resins in this process - including incomplete layer consolidation and parts with lower density, dimensional inconsistencies and sub-optimal physical properties. Using Sabic’s proprietary technologies, the company has demonstrated the ability to produce fully amorphous parts with part densities above 96 percent, good dimensional stability and low refresh rates.