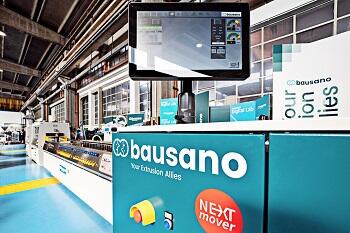
Sustainability is now a key concept that affects all economic sectors, first and foremost construction, where attention is increasingly required when dealing with innovative and eco-sustainable materials, also for interior furnishings. In this respect, Bausano responds to the new needs of the sector, enhancing its extrusion lines for plastic waste (PVC, PE or PP) and natural fibres, including wood dust and substances of plant origin, such as rice husks, coffee grounds, banana peels, seaweed, almond shells, avocado kernels, cork and other plant residues.
The market for composites obtained from natural fibres is experiencing significant growth thanks to the properties that make these materials unique in terms of versatility, reliability and environmental impact. In fact, they are 100% recyclable and can be transformed into a new product at low cost. By virtue of their exceptional performance characteristics, in terms of high resistance to corrosion, atmospheric agents, UV rays and impermeability, they are ideal for cladding, furniture and indoor and outdoor flooring, especially decking. Furthermore, thanks to their increased lifespan, plant fibre-plastic composite materials are also increasingly used in the automotive sector, for the internal lining of door panels, dashboards, trunks and for the production of particularly light components, which contribute to reduce the weight of vehicles.
Bausano’s extrusion technology has been perfected to incorporate up to 100 phr of wood or natural fibre. The specific counter-rotating twin-screw configuration makes it possible to achieve an accurate mixing between melted polymer and fibre, passing it through the mould without the need for a melting pump. Specifically, profiles can be directly extruded from the raw material (direct extrusion) or the material can be processed starting from the granule (indirect extrusion). In direct extrusion, Bausano machines ensure the processing of fibres with a humidity level of up to 12% at a speed three times higher with respect to other solutions on the market. The granulation lines, specifically designed to ensure maximum performance at any production speed, also enable the use of recycling materials and can be configured with premixing or gravimetric dosing systems upstream. The granules obtained can thus be transformed into a finished product either through moulding or extrusion, with twin or single screw. Lastly, the lines are distinguished by the high degree of customisation, the wide range of modular accessories and a special coating, on request, which extends the useful lifespan of screws and cylinders up to 25,000 hours, before replacement is required.
“The plant fibre-plastic composite materials are a valid alternative in construction and architecture. In fact, they are part of a circular economy perspective: for example, the wood used is usually a product of waste from the furniture industry that is recycled to be extruded again, thus limiting deforestation” and continues “Europe is currently the third largest market in the world for wood-plastic composites and I believe that EU policies for the environment and climate provide significant opportunities for the growth of the sector, in particular through the “Renovation Wave” strategy, an integral part of the Green Deal promoted by Brussels. For Bausano, enhancing this range of extruders is part of a broader programme, aimed at pursuing the sustainable development goals drafted in the United Nations 2030 Agenda. A path that sees us engaged on three levels: social, environmental and economic, acting as the spokespeople for a virtuous change that also involves our customers”, Clemente Bausano, vice president of the company stated.