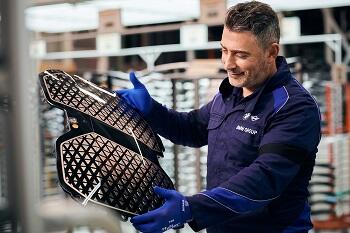
The BMW Group has launched a new Engel production unit at its Landshut production plant. The kidney-shaped badge for the electric BMW iX is produced in a cleanroom atmosphere. Both the BMW Group and ENGEL are breaking completely new ground here, prompting the International Society for Plastics Technology (SPE Central Europe) to honour the application with the SPE Grand Award 2021.
Once the radiator grille, this characteristic design feature of all BMW models has taken on a new role following electrification of the drivetrains. The kidney-shaped badge protects the camera as well as several sensors for assisted and, in future, autonomous driving. The new function means that both the design and the manufacturing process for the kidney-shaped badge has changed fundamentally. In an integrated process, a heatable functional film is back-moulded with polycarbonate and flood-coated with polyurethane. This is a combination of processes which is also offered by Engel under the name clearmelt. The sensitive electronics are well protected under the scratch-resistant polyurethane surface. The high gloss level and depth effect, which even a thin coating of polyurethane achieves, convey a very elegant impression.
The production cell integrates an Engel duo combi M injection moulding machine with a horizontal rotary table, two large articulated robots for handling the films and moulded parts, a film cleaning system, an inline quality-control station and peripheral units including polyurethane technology. The injection moulding machine's clamping unit and the robot work areas are encapsulated over a length of six metres and a height of more than four metres to achieve an ISO class 7 cleanroom. The special feature: Above the injection moulding machine, the cleanroom has a sliding ceiling which can be opened for mould changes and other work in the mould area. All work steps in the cleanroom are automated. The robots also unpack the function films and pack the parts.