Sviluppo congiunto di una cella di stampaggio per test con polimeri ad alte prestazioni
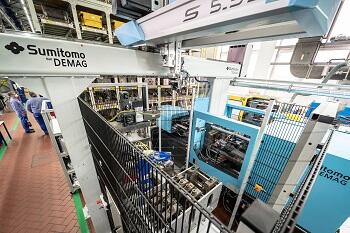
Nel reparto pilota per lo stampaggio a iniezione presso la sede di Basf a Ludwigshafen (Germania) è stata messa in funzione una cella di produzione completamente automatizzata basata sulla pressa elettrica IntElect 1000 kN di Sumitomo (SHI) Demag per l’esecuzione di oltre 4000 test all’anno per lo sviluppo congiunto di materiali e applicazioni. La pressa a iniezione di Sumitomo (SHI) Demag è stata scelta, in particolare per il design compatto, l’efficienza energetica e la ripetibilità di processo, cui si aggiungono cambio stampo automatizzato, ridotto inquinamento acustico e robotica completamente digitalizzata.
Un robot lineare SDR 5-35S consente di automatizzare completamente la selezione e il posizionamento di 12 inserti intercambiabili dello stampo da un magazzino situato all’interno della cella stessa. Una volta che il componente è stato stampato lo stesso robot, dotato di pinza multifunzione, lo estrae e lo trasferisce a un robot Yaskawa GP8 a sei assi con braccio articolato per il taglio preciso dei provini per mezzo di una punzonatrice con servomandrino. La cella include anche un’unità di controllo della temperatura e un nuovo MES (Manufacturing Execution System) digitale per mappare ogni sequenza dei test.
Molti dei campioni sono realizzati con termoplastici per applicazioni ad alte temperature rinforzati con fibre e in molti casi anche con ritardanti di fiamma. Di conseguenza, le temperature di fusione possono arrivare a 400° C, con stampi che raggiungono i 180° C. Il magazzino può contenere fino a 12 inserti intercambiabili che possono essere sostituiti in qualsiasi momento nella pressa. L’integrazione di un sistema di controllo della temperature HB-Therm con il sistema di controllo della macchina rende possibile effettuare il cambio automatico degli inserti nello stampo in modo sicuro ed efficiente anche con un processo ad alte temperature come in questo caso.
Il MES informa la cella quando la produzione del campione corrente è prossima al termine, così che venga preparato quello per la successiva applicazione. Immediatamente dopo la fine del processo di iniezione, il raffreddamento dell’inserto dello stampo è diretto dall’interfaccia dell’unità di controllo della temperatura integrata. A questo punto, il cambio degli inserti dello stampo viene sincronizzato con il controllo della cella tramite segnali di ingresso e uscita, trasmettendo i nuovi dati tramite l’interfaccia del robot. Dopo il cambio dell’inserto, i termoregolatori vengono nuovamente riscaldati e non appena raggiunta la temperatura inizia il nuovo ciclo di stampaggio.
Tutti i provini sono realizzati in conformità allo standard ISO 294, che specifica la precisione che il sistema di colata deve garantire e i requisiti geometrici che ogni campione deve possedere. A questo fine la rimozione mediante punzonatura non modifica le proprietà da materiale ed elimina qualsiasi particella di polvere presente. La pinza multifunzione assicura che tutti i campioni siano posizionati sulla piastra di punzonatura con la massima precisione in base alla loro geometria, operazione complessa data la vasta gamma di materiali utilizzati e la presenza della fibra di rinforzo, che può essere causa di deformazioni.
Trattandosi di un progetto pilota, sulla macchina vengono impostati fino a 20 test al giorno, il che implica che il programma di controllo della cella deve essere adatto a diversi materiali, geometrie dei campioni, temperature e parametri di processo. Ogni singola ricetta eseguita viene quindi registrata e documentata in digitale.