Ecco Radilon NeXTreme, per applicazioni ad alte temperature
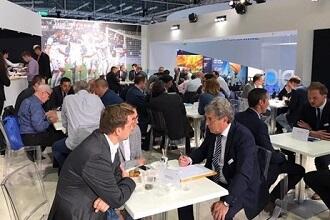
A base poliammidica, il nuovo Radilon NeXTreme presentato da RadiciGroup al K 2019 è ideale per l’esposizione a temperature elevate. “È un prodotto che abbiamo sviluppato inizialmente per applicazioni in ambito automobilistico, grazie alla eccezionale resistenza all’invecchiamento termico a seguito di esposizione in continuo con aria a 230°C. Usando la stessa base polimerica abbiamo poi sviluppato anche una versione per l’estrusione di filamenti tecnici per applicazioni industriali, dove sono previste condizioni di utilizzo molto severe”, ha spiegato Erico Spini (nella foto al centro), global marketing manager di RadiciGroup High Performance Polymers, nel corso della conferenza stampa di presentazione del prodotto.
Due le versioni del nuovo Radilon NeXTreme destinate al settore auto: rinforzato con il 35% fibra di vetro (RV350HHR 3800 BK) oppure con una carica del 50% (RV500HHR 3800 BK). Le applicazioni tipiche riguardano componenti del sistema di aspirazione dell’aria dove è richiesta una notevole resistenza termica.
“C’è poi una terza versione, il Radilon NeXTreme HSW 100 NT, per estrusione di monofilamenti tecnici, già testato con successo sia nel processo di estrusione sia in applicazioni concrete (spazzole professionali per uso industriale, spazzole per la pulizia dei metalli in sostituzione della fibra naturale “tampico”, spazzole professionali per parrucchieri) laddove è richiesta una elevata prestazione termica”, ha aggiunto spini.
“La presenza di nostri stabilimenti in tre continenti fa di
noi una azienda globale, rafforzata dall’integrazione verticale nella filiera
della poliammide. Fare parte di RadiciGroup ci consente di mettere in atto
importanti sinergie, dall’R&D al recupero di scarti di produzione, con un
approccio strategico alla sostenibilità”, ha sottolineato Cesare Clausi (nella
foto in basso), global sales manager di RadiciGroup High Performance Polymers
in occasione della conferenza stampa.
Per quanto riguarda i settori di applicazione, le attività di ricerca e innovazione di RadiciGroup High Performance Polymers si sono concentrate recentemente sull’e-mobility, mercato in forte espansione per il quale la necessità di alleggerimento, e quindi di sostituzione dei metalli, è ancora più importante rispetto ai veicoli tradizionali al fine di aumentarne l’autonomia.
Materiali resistenti alla fiamma a base poliammidica privi di alogeni e di fosforo rosso, come Radiflam A (PA 66) e Radiflam S (PA 6), vengono già utilizzati per auto, veicoli pesanti, motociclette e bici elettriche, a cominciare da molti componenti del sistema batteria, fino ai connettori e parti di inverter. La gestione termica di un veicolo elettrico è particolarmente importante perché da essa dipende il rendimento del sistema nel suo complesso. In fiera RadiciGroup presenta soluzioni con prodotti standard (Radilon A, PA66 resistente all’idrolisi) e innovativi come Radilon D (PA610, parzialmente da fonte biologica), Radilon DT (PA612), Radilon Aestus T1 (PPA) e Raditeck (PPS).
Per il mercato automobilistico più tradizionale RadiciGroup High Performance Polymers sta proponendo soluzioni in PA 612 (Radilon DT) e PA 610 (Radilon D) in sostituzione della PA 12. Questa scelta è giustificata dalla necessità di disporre di materiali capaci di resistere a temperature di utilizzo in continuo superiori, per diversi segmenti auto, rispetto alle PA12 tradizionali. Alla fiera K vengono presentati nuovi materiali specifici per condotti aria, condotti circuito di raffreddamento, condotti TOC, condotti SCR e tubi carburante capaci di superare test in aria e benzine fino a 120-130°C in continuo.
Il K 2019 è una vetrina anche per alcune nuove specialità
dedicate al settore idrotermosanitario. “È un comparto in cui stiamo lavorando
in misura crescente e in fiera presentiamo nuovi materiali adatti al contatto
con acqua potabile secondo quanto prescritto dalle norme WRAS (Regno Unito),
W270 DVGW e KTW (Germania), ACS (Francia) e US (NSF 61). Abbiamo messo a punto
delle poliftalammidi (Radilon Aestus T1 RKC) per contatto con acqua calda,
approvate secondo la norma KTW a 85°C nonché versioni speciali della PA 612
(Radilon DT RKC2) caratterizzate da elevata resistenza all’idrolisi, ottima
fluidità e omologata KTW per contatto con acqua calda fino a 60°C, infine
versioni su base PA66 (Radilon A RKC2) a migliorata resistenza alla
termo-ossidazione”, ha proseguito Erico Spini.
Sempre a base di poliftalammide (Radilon Aestus T1 FC) sono i materiali speciali adatti al contatto con gli alimenti, che superano i test specifici per questo settore (norma EU
10/2011) a seguito di contatto prolungato con i cibi alle alte temperature: in questo caso le parole d’ordine sono sicurezza e tutela della salute.
La sostenibilità, infine, è da sempre strategica per RadiciGroup: in questa direzione nel 2018 il gruppo, High Performance Polymers in primis, ha aderito al programma Operation Clean Sweep promosso da Plastics Europe con l’obiettivo di prevenire dispersioni di polveri e granuli nell’ambiente. Un impegno che, a cascata, sta coinvolgendo anche le altre divisioni di RadiciGroup. Questi temi saranno al centro del wworkshop “Zero Pellet Loss. A value chain commitment” che RadiciGroup terrà al K il 22 ottobre.