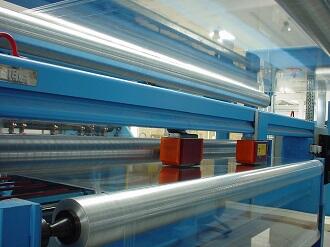
The solutions offered by Electronic Systems for measuring and quality control systems, designed in particular with extrusion and calender lines in mind, are always developed on the basis of solid scientific foundations. At the same time, they are easy to use even for operators without a high level of training and specialisation.
This manufacturer from Momo, near Novara (Italy), has made a number of technological developments for its range of measurement devices, including the pneumatic-induction technology, which has been highly successful over the past decade. It is used in the ESSAIR product line (namely Electronic SystemS AIR) where the thickness of plastic laminate is measured using what is defined, though somewhat emphatically, as “divine” blowing, an absolutely innocuous, light blow of air which is, therefore, as environmentally friendly and safe as one might hope. No ionising radiation, no contact with the material being measured. But more significantly, thanks to a patented concept, the company has developed a sensor that is able to self-calibrate, thereby skipping over the human component that can affect the outcome of complicated calibration procedures.
The simple, basic idea however required notable commitment before developing a device with suitable operating characteristics, even in particularly demanding industrial environments. Thanks to continuous improvement in performance and usage methods, this technology has found increasingly wider application scope for large scale use in a variety of production processes, spanning from extrusion to calendering and coating in their most extensive ranges. The measurement is done on materials like PVC, rubber, polymer film with various structures and expanded resins of different colours and complex formulas, without affecting the outcome. The diversity of the processing methods and specific measuring and control needs has been a source of inspiration for introducing new, innovative models.
In fact, using a number of sensors in self-calibrating versions for fixed positions, the company has set a new standard in the rubber calendering sector. This has led to advantages even in automatic thickness control, with consequent savings in raw materials.
Today, it is also possible to measure a PVC sheet directly on one of the calendering cylinders where, until now, temperature and chemically aggressive environments have prevented the use of more traditional technology. For this application, together with the development of a new version of the pneumatic-induction sensor, a scanner has been developed to operate in high temperature environments, with particularly aggressive vapours and coating calenders with widths in excess of 4 metres.