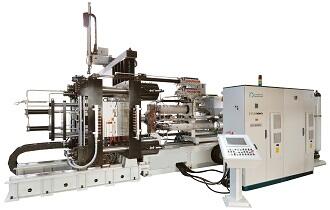
An injection moulding machine with a clamping force of 1,600 tons, capable of co-injecting a total shot weight of 20 kg (sandwich structure) has been recently supplied by Presma to an Italian processor. This machine is equipped with an automatic moulding cell and can optimize the production of large items in bicomponent material (solid/foam), that is already carried out using Presma machines, but of the rotary, multi-station type.
This supply represents the first example of a medium-sized single-station machine equipped with the special “BIC” injection unit that, ever since it was patented in 1981, has been offered by this Italian company for the moulding of articles with high thicknesses.
Co-injection, or two-component moulding, is the technology that allows the simultaneous injection, through the same nozzle, of two materials: in this case, a solid one, and one containing chemical foaming agents. This technique makes it possible to obtain high-thickness articles that have a skin in solid material and a core in expanded material, thereby eliminating the problem of deformations, cracks, areas of shrinkage, and many of the problems typical of high-density articles moulded in the conventional way. Co-injection is a justified choice for articles thicker than 5 mm that need a smooth and shiny surface. Considering that for the exterior a high-quality material is required, while an inferior quality or recycled material can suffice as a filler, it is clear that there are considerable savings to be made. Further savings can be obtained from the colorant, which is needed only for the external material.
The costs generated by the long moulding cycles needed for products of a certain thickness can be broken down intelligently if one exploits the possibility of working on multiple moulds and varying the model of the product. This is one of the most important advantages of combining co-injection with a multi-station system. The need to have single-station versions on hand as well is dictated by the fact that some articles have to be produced in different colours and/or different materials, and, in such cases, no series of moulds are provided. These are articles that have to be made according to a special design and with reduced thicknesses and must, in any case, guarantee structural elasticity. In these situations, it is crucial to combine a solid material for the surface with a foamed one for the core, and in this way it is also possible to obtain excellent aesthetics and advantages in terms of the appeal of the product and its costs.
In the first week of September a second single-station machine, also for co-injection moulding, was delivered to the same processor. This is a 400-ton machine with an injection capacity of 7,800 cm3 and it is destined to the moulding of items with low thicknesses that do not need long cooling times.