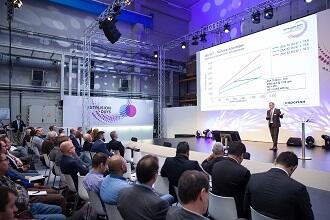
Over 200 participants from approximately 25 nations came to Stuttgart, Germany on November 15 and 16, accepting their invitations to the Coperion Extrusion Days. In keeping with the motto “Efficiency in Compounding”, lectures, factory tours, and live presentations acquainted visitors with the enormous potential that modern extrusion technology provides for optimizing production processes involved in engineering plastics compounding. Significant throughput increases together with time and operational cost savings - without compromising product quality - comprised the focus of these events.
Within the framework of this two-day event, internal and external experts from industry and research provided background information on the efficiency of the twin screw extruder and its peripheral devices, as well as on special developments for a broad range of diverse applications. Practical examples of successfully implemented optimization processes were central to the event.
Among the demonstration highlights was the production of an anti-block masterbatch using a ZSK 58 Mc18 twin screw extruder and Coperion’s patented, throughput-increasing Feed Enhancement Technology (FET), expanded with a semiautomatic SCP strand conveying unit, as well as a SP 200 strand pelletizer from Coperion Pelletizing Technology.
A ZSK 34 Mv PLUS twin screw extruder was the central element in a demonstration of HMPSA (Hot Melt Pressure-Sensitive Adhesive) manufacturing. In this example, a Roll-ex system masticated rubber balls on hand as a formula component so far as to enable continuous extruder feeding.
Use of a demonstration extruder with a transparent plastic housing allowed Coperion Stuttgart's research and development team to give visitors the ability to see for themselves how differently designed mixing elements ensure complete mixing of two fluids with different viscosities. A CFD (Computational Fluid Dynamics) flow simulation shown in parallel demonstrated the broad agreement between theory and practice. Coperion is implementing this process in order to evaluate newly developed screw elements and mixtures, among others.
“More efficient processes with higher
throughputs are the alpha and omega of modern engineering plastics production.
For many years, we have been tailoring our technical developments in
compounding processes with the goal of increased efficiency. Using individual
machines, complete turnkey systems, and process know-how gleaned over decades,
we offer our customers a broad spectrum of options for optimizing their
production”, said Peter von Hoffmann, General Manager, Business Unit
Engineering Plastics & Special Applications at Coperion.
The variety of questions raised in the forum, as well as the animated discussions during breaks between event blocks, demonstrated how great the need is for information in this field. Time and again, participants expressed amazement at the versatile possibilities shown, even in their own companies, to increase productivity with short-term ROI and increased quality consistency.
Moreover, during one extensive factory tour, participants at the 2018 Extrusion Days gleaned an impression of Coperion’s vertical integration at its Stuttgart location, ranging from screw element and extruder barrel manufacturing to final assembly of twin screw extruders.