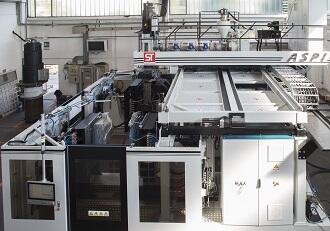
When the production of blow moulded industrial items is high, is it better to choose more single-cavity machines, thus multiplying the cost of investment, the floor space and energy consumption, or a multi-cavity machine, which minimizes all these costs, but makes production less flexible? In order to answer this question, ST Blow Moulding designed Aspi 150.3 DUO for the production of 3D articles blown using the parison suction process, which doubles the production output of a single-cavity machine without doubling its investment and operating costs, whilst at the same time providing great flexibility of use.
Like all the models of the Aspi series, the DUO can also be used for 2D blow-moulding: each clamping unit is in fact fitted for the installation of a bottom-up blowing unit (optional), complete with nozzle and spreaders.
The machine structure is based on two side-by-side clamping units and an accumulator extrusion head which moves, together with the related extruder, on the upper platform, to alternately feed the two moulds according to the cycle rate. It is a solution that provides for a very small machine footprint (the clamping units are static: no movement tracks, no pipes that move back and forth and no cable chain); moreover, it offers perfect accessibility to the moulds (the tiebarless clamping units are accessible from both sides) and high quality consistency (since a single extrusion head guarantees maximum production uniformity).
As regards the flexibility of production, the cycle parameters can be set separately for each of the two moulds, such that the machine can handle two different recipes at the same time. When production needs require it, two different moulds can therefore be mounted to fully exploit the machine's potential.
Perfect compromise between high production rates and quality and flexibility, the first Aspi 150.3 DUO was recently installed in the USA.