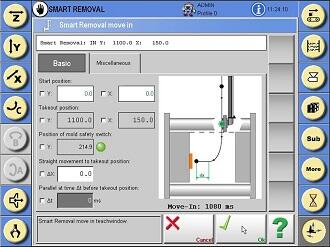
Minimization of unproductive downtimes is a top priority for injection moulding machine operators, since this is the only way to have the investment in the machine amortized in the shortest possible time. The Wittmann W8 and WX robot generations come with the patented SmartRemoval function as standard, which automatically shortens the time required for parts removal from the mould area without any operator intervention.
The advantages are obvious: shortening of the unproductive time plus lower total energy consumption for the system through reduction of the heat loss caused by the mould standing open for any length of time, which ultimately also contributes to more consistent process quality. Here, the injection moulding process as such is basically left completely untouched, since SmartRemoval only influences the time required to remove the part from the machine. All parameters set on the processing machine remain unchanged.
The R8 and R9 robot control systems from Wittmann automatically calculate from the first cycle how long the mould opening movement will take. Then, in all subsequent parts removal processes, the system no longer waits for the complete opening of the moving mould half, but instead already starts to move the vertical axis of the Wittmann robot beforehand, just like the “flying start” known from motor sport. At the moment when the mould is fully opened, the axis is already moving at an optimal speed and can be accelerated still further for the actual removal process inside the open mould area. So, in contrast to the conventional sequential removal process, the gripper of the robot arrives earlier at the position where the transfer of the moulded part takes place.
The
synchronization with the ejectors functions in a similar way. Based on previous
automatic measurements, the Wittmann robot already issues the ejector signal
before it arrives at the parts removal position, so that when it reaches that
position it can take over the parts directly without having to wait for the
ejectors’ response. This process is designated as “Move In”. In the subsequent
“Move Out” phase, the ideal timing to send the machine the “close mould” signal
- before the Wittmann robot has moved completely out of the mould area - is
calculated in a similar way. The aim of these measures is to eliminate from the
process the delays caused by electrical signal transmission. The patented
SmartRemoval function is included in the standard scope of delivery for Wittmann
R8 and R9 control systems.