Bivite corotante per riciclo e compounding
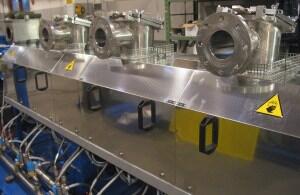
L'impiego di estrusori bivite corotanti di Comac nel settore del riciclo è andato aumentando negli ultimi anni, dopo che per lungo tempo le loro principali applicazioni erano state in impianti per la produzione di masterbatche e per il compounding. Gli estrusori monovite, meno costosi, infatti, sono spesso preferiti nel campo del puro riciclo per così dire non critico, dove l'impiego di quelli bivite corotanti non è giustificato. A favore di questi ultimi, però, si stanno affermando in maniera sempre più marcata due filoni d'impiego. Uno è rappresentato dal riciclo delle scaglie ricavate dalle bottiglie in PET post consumo che, grazie all'elevata capacità di degasaggio assicurato dell'estrusore bivite corotante, possono essere lavorate senza essiccazione. Si ottiene così un materiale adatto a svariate applicazioni quali, per esempio, la produzione di fibra o di foglie e lastre per termoformatura e la rigranulazione. L'altro filone è costituito dal riciclo di materiali da scarti industriali a base poliolefinica.
Se gli impianti di Comac trovano da sempre impiego nel compounding di polimeri con cariche e rinforzi di vario tipo, l'implementazione di configurazioni particolari, quali, per esempio, quelle cosiddette "tandem" (ossia costituite da due estrusori in cascata tra i quali è interposto un sistema di filtrazione), ha rappresentato la soluzione ideale per riciclo più compounding partendo da materiali molto difficili da trattare, come i film pesantemente stampati con inchiostri a solventi chimici. Questo tipo di impianti consente di effettuare l'estrazione delle sostanze volatili, una filtrazione molto spinta, l'aggiunta di materie prime vergini, cariche, masterbatch ecc. e la rigranulazione, ottenendo un materiale riciclato e caricato di qualità elevata. Tutto ciò sarebbe difficilmente realizzabile con gli estrusori monovite.
Per il riciclo di PET, la società propone generalmente linee da 40 a 44 diametri, dotate di 3 zone di degasaggio con sistema del vuoto più o meno spinto, a seconda delle caratteristiche che si devono conferire al prodotto finale. Nel caso delle poliolefine, invece, la configurazione tandem prevede un primo estrusore dove avviene la plastificazione del materiale da riciclare, un primo degasaggio e la prefiltrazione del fuso. Questo passa quindi in un secondo estrusore più lungo nel quale vengono aggiunti materiali vergini o meno contaminati, masterbatch colorati, cariche e additivi; tale estrusore è dotato di alimentatori laterali, di vari punti di degasaggio atmosferico e sottovuoto, di un dispositivo di filtrazione finale e di taglio in testa.
Le linee per il trattamento delle scaglie di bottiglie in PET post consumo senza essiccazione sono state fin qui realizzate in versioni con estrusori di diametro da 40 a 120 mm, che si traducono in un ventaglio di capacità produttive comprese tra 100 e 130 kg/ora e oltre 1500 kg/ora. Le versioni più frequenti in questo caso sono quelle da 70 mm, in grado di assicurare una resa di 500-550 kg/ora. Nel caso del riciclo di scarti a base poliolefinica, con la versione da 120 mm si ottengono produttività nell'ordine dei 2000 kg/ora, che risultano anche più elevate con il nuovo modello da 135 mm, da poco entrato a far parte dell'offerta di Comac.