Two tracks for draw-tape bags on roll
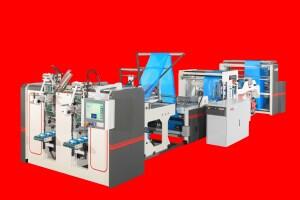
The new Roll-Flex Draw-Tape bag-making machine, characterised by two independent tracks, instead of one, developed by Saldoflex for the production of draw-tape bags on roll has been recently delivered to a primary European converting company. This machine sums up all the improvements recently seen on the Roll-Flex series. First of all, it is marked by total flexibility, thanks to the possibility to work either on one or two tracks at the same time and to shift from bottom seal to double seal directly from the operator panel during operation, without any further intervention on the machine. This machine makes it possible to produce gusseted, star-seal, no-drop side-seal, "C"-folding and double "V"-folding bags.
It is provided with two independent draw-tape unwinding systems (for each of the two tracks) with automatic change, each one consisting of two motorized unwinders as well as an accumulating and on-the-fly changeover unit, allowing for the change of the draw-tape reel without any need to stop or even slow down production. The sealing bar with special design enables an extremely quick replacement of the teflon tape (less than 2 minutes). The machine features a servo-controlled pre-cut blade and an electronic micrometrical adjustment system of the pre-cut depth, which is controlled directly from the operator panel during production, without any manual intervention on the machine and with the possibility to save the pre-cut depth value in the process recipe.
The automatic revolver rewinder, which works on two completely independent tracks operated by two specific servomotors and controlled by two independent driving systems, grants the best control of tensioning and speed on each track, also in case the thickness of the starting film is not uniform. Further significant enhancements, leading to great improvements in terms of noise, speed, precision and ease of maintenance, include the new drivetrain system to the winding spindles by means of toothed belts instead of gears, as well as the innovative movement for roll extraction, which is now servo-driven instead of pneumatic.
The rewinding cycle can rely on 4 stations/shafts for each of the two tracks, allowing the four winding phases, pre-cut tear-off, taping and roll removal operations to be performed simultaneously. In order to grant a very high productivity also when producing rolls with a low bag count, it is possible to carry out up to 25 roll changes per minute (complete with taping).
The taping units are provided with water metering and dosing system by means of a rubber and an engraved anilox roller. It allows the best accuracy and repeatability in adjusting the quantity of water deposited on gummed paper regardless of the machine speed, thus making it possible to eliminate waste, avoid any issue related to insufficient or excessive amount of water, and facilitate the proper dosing for every type of gummed paper. Also the three-track version offers all the above-mentioned technical characteristics, except for the specific solutions intended for the production of draw-tape bags.