Gefran enhances the range of Hyperwave contactless position transducers
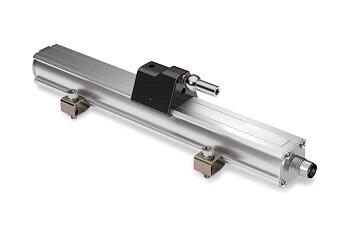
The Italian multinational group specialised in the design and production of sensors, industrial process control systems, electric drives and automation components, Gefran, enhances the range of Hyperwave contactless magnetostrictive position transducers with the launch of the WPL (HyperWave Profile IO-Link) series equipped with IO-Link 1.1 interface, which guarantees optimised integration and communication with the new 4.0 architectures typically used in medium-to-large size machines used for a broad range of applications in industry such as plastic, aluminium, metal, wood, ceramics, and glass.
“The constant evolution of technologies in the 4.0 Industry and IoT setting is encouraging the adoption of standard communication protocols, such as IO-Link in industrial automation, thanks to the numerous advantages it offers compared to traditional analogue connections. If in the past sensors only sent simple commutation and measurement signals, they are now required to process an increasing amount of information, even on diagnostics. With this regard, the WPL series becomes the ideal answer to the needs of OEMs and End users seeking highly performing solutions that are compatible with most industrial fieldbuses”, states Edoardo Zilioli, Sensors Marketing Manager at Gefran.
Thanks to the characteristics of an enhanced digital connectivity, WPL smart sensors stand out in particular for their ability to collect a higher quantity of process data and for rapidly and safely transmitting them in digital mode, with error bits and bytes to check data consistency (checksum). The accurate interpretation of a larger amount of information translates into a concrete advantage for clients in terms of preventative and predictive maintenance of both the sensor and the machine, favouring an increase in the efficiency of the entire process. Moreover, replacement is particularly fast because the IO-Link master reconfigures parameters making them suitable to the new sensor. Additionally, the standardised IO-Link connection cables, which are easily accessible on the market and ready-to-use, guarantee a simplified installation.
WPL magnetostrictive transducers are the only transducers on the market capable of providing cyclic data on cursor position and speed of movement and are available in a version with two SSC (Switching Signal Channel) outputs, which are useful to set control or alarm thresholds. Sensor acquisition of acyclic information is also noteworthy, as such data are valuable for machine manufacturers to evaluate machine state of use and potential breakdowns and thus improve the design of following series, as well as for end users, to maintain the machine in perfect conditions and identify error causes in case of repair. More specifically, the WPL series memorises the number of travelled km and time in movement, which makes scheduling regular maintenance (e.g. lubrication, gasket replacement, cleaning) much easier. Moreover, it enables to record maximum speed and acceleration, with the goal of identifying the potential causes behind the production of abnormal batches, as well as the highest temperature reached by the machine, to optimise settings and avoid over-temperatures that might lead to false or missed cursor readings. Finally, this set of features is completed by the detection of out-of-range movement, i.e. the movement of the cursor out of operating range due to a loss of signal of as little as few mSecs that cannot be detected by the PLC.
“The new cULus certified sensors with IO-Link output share with the rest of the product range the advantages deriving from Hyperwave magnetostrictive technology in terms of a signal amplification 15 times greater than traditional models, resolution inferior to 0.5µm and high measurement stability, even in presence of various typical field disturbances such as shock, vibration, EMC disturbances and thermal drift. Thanks to the IO-Link interface, the WPL series is a concentration of technology that requires a limited investment from customer side, completely in line with components used for the transduction of an analogue signal or with an electric circuit for fieldbus communication”, concludes Zilioli.