Amut returns to Australia with a post consumer PET bottle recycling plant
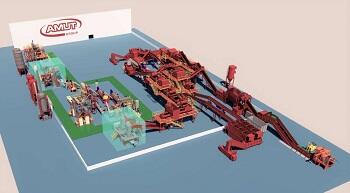
In 2000 Amut had delivered to Coca Cola Amatil in New South Wales, Australia, one of the first plants in the world for the recycling of post consumer PET bottles destined for the production of food rPET, thus starting the "bottle-to -bottle ". In recent years, however, China and South East Asia in general have banned imports of plastic waste, so that countries like Australia itself had some problems to manage those produced internally, also in light of the principles of circular economy.
At the beginning of 2019, three major Australian companies active in different markets such as rigid packaging, beverage, waste management and recycling, started to cooperate putting in common their ideas with the final goal of giving a second life to post consumer PET bottles collected in the various Australian MRF. This gave birth to one of the most prestigious projects about the PET bottles recycling in Australia, considering the requested capacity of about 23,000 tons per year of rPET and the flexibility of a plant able to process bottles coming from the different MRF, therefore containing a wide range of contaminants.
Also in this case Amut has been chosen as turnkey supplier of a plant of high technological level for selecting and recycling post consumer PET bottles and able to grant the capacity and flexibility for treating the required volumes and materials containing different contaminants. With a closer look into the specifics, the selection and washing line will include an automatic system to remove the iron wire from the bottles bales, the Amut patented machine for the dry removal of all labels and an automatic selection system, by means of NIR sorters, to separate the following items from the mainupstream: PO bottles, PET coloured bottles, PET containers or trays, aluminium containers and cans. All these contaminants will be separated and stored in suitable bunkers where, later, they will be pressed in bales according to their second use.
Moreover, to ensure the complete removal of the so-called pressure adhesive labels and hot melt glue, together with all organic contaminants, the plant will be equipped with a double Friction Washer, the Amut patented machine. Also the PO, mainly coming from caps, will be fully recovered. Thanks to the presence of two separation troughs, placed before and after the two Friction Washers, polyolefins will be then dried by means of a centrifuge and separated from any possible labels residual by means of an air separation system, to be eventually stored in suitable big-bags. In order to reduce the fines quantity in the material, there will be a second grinding for the flakes so-called oversize that will then enter the mixing silos and the flakes control later, by means of the NIR detectors acting on polymers, colours and metals. Last but not least, the plant will give the possibility to process also batches of PET containers and trays with a low viscosity rate.
The plant will be installed in the Victoria State, with a production timeline set by the end of 2021.