Production efficiency and energy saving for the automotive industry
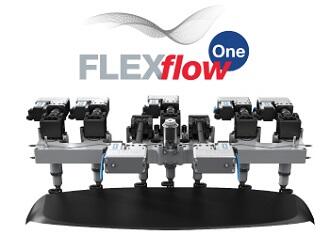
Among the novelties introduced by HRSflow at the K 2016 fair, FLEXflow One represents the further development of FLEXflow. It is an electric servo driven valve gate system where control unit is not required anymore. The new system includes a fully integrated electrical box, and the electrical motor, used to control the valve pin movement, improves the injection process and provides better part quality.
All the process parameters can be set by a space-saving, easy to use ESI - External Smart Interface. Among the benefits of this electrical solution: repeatable process, safety, cleanliness, ease of use, reduced footprint and process traceability.
During the show, the market also saw the launch of ECOflow, a new environmentally-friendly hot runner system, which assures a significant energy efficiency and a reduced system size, considering that the weight and volume of the manifold have been lowered in over-all size, and energy consumed is therefore reduced. These features also reduce the time necessary to reach a uniform and stationary operating state. As regards energy efficiency and thermal stability, the new ECOflow line allows energy consumption to be reduced up to 25%.
Along with these innovations, HRSflow also introduced some technical updates. HP Gate is a new gate suitable to process technical materials such as PMMA. The new geometry simplifies the seat in the mold, so that the optimal result is now determined by the nozzle and not by the mold anymore. Among the main benefits of this solution are: improved gate quality, no stagnating material between tip and mold, simplification of the mold cut out and a wider process window.
Made of three materials, the 3 Layer Tip features a copper layer, improving its thermal conductivity. Thanks to the use of a special steel and the removal of any coating, this solution ensures an optimal wear and abrasion resistance, eliminating black spots on the molded parts.
Pressure Block is made with special low heat conductible materials. It is positioned on the hot runner manifolds, between the system and the mold, to increase the plate stiffness under load, keeping an optimal thermal profile along the whole hot runner system. The main feature is the flexible positioning without negatively affecting the thermal profile of the hot runner system.
Finally, the thread safe kit is a special bushing positioned between nozzle and manifold thread, in order to accommodate easy nozzle removal when processing materials such as PMMA and PC. It eliminates the seizing between nozzle and the manifold, allowing for simple removal of the nozzle from the manifold for routine maintenance.