Power backflush technology keeps flow and pressure constant
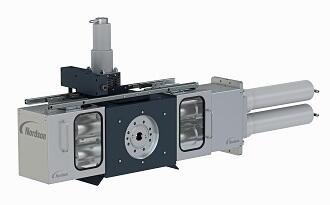
Nordson Corporation has enhanced the design of its patented “power backflush” V-Type screen changer, creating a more compact and efficient system whose continuous operation eliminates downtime in extrusion, pelletizing, and recycling. Nordson’s BKG HiCon V-Type 3G screen changer uses a hydraulically powered backflush system to automatically remove contaminant while maintaining extrusion throughput and keeping flow and pressure constant. Operationally, the new screen changer is more streamlined and efficient than the earlier V-Type system from Nordson, with a 30% shorter backflush cycle. There is a higher degree of automation resulting from an autonomous parameterizing of the entire backflush procedure and of the screen change procedure, including filling and venting.
All of the filtration area of the combined four screen cavities is available for production while filling of the displacement-piston cylinder takes place. Two outlets for backflushed material are located on the bottom of the unit, with discharge automatically controlled by the movement of the screen-bearing pistons.
In comparison with the earlier V-Type system, the height of the new V-Type 3G screen changer has been reduced by 30%, permitting a lower extrusion height; a single displacement piston is used for backflushing instead of having one for each screen cavity; and hydraulic piping has been optimized.
“The HiCon V-Type 3G screen changer provides up to 200 backflushing cycles before screens must be changed, reducing operating costs”, said Christian Schroeder, global product manager for melt delivery products. “With four screen cavities making a large filtration area available in a comparatively small housing, only minimal amounts of material are lost in backflushing”.
In the HiCon V-Type 3G screen changer, melt flow from the extruder is split at the entry side and guided to the four screen cavities, two of which are located on each piston. Each pair of cavities is positioned so that they can filter their respective melt streams, until the piston removes one of the cavities from the process to remove contaminant buildup by means of backflushing. In normal operation, polymer is flowing through all four cavities. While one of the cavities is changed, the other three remain in the process.
In addition to the two screen-bearing pistons, there is a single hydraulically actuated displacement piston that operates during backflushing. When the differential pressure across the screen changer increases to a pre-set level because of contaminant buildup, the backflush sequence for all cavities will be started automatically. For each cavity, the displacement piston retracts, creating a reservoir of filtered molten polymer. This material is hydraulically compressed and discharged in reverse direction, back through the screen, carrying away contaminant for removal from the system. The sequence is performed for each cavity one after the other.
“Our new backflush screen changer is suitable for almost all processes and materials”, said Schroeder, “including processes with strict requirements for constant pressure, such as strapping, film, fiber, and processes with insufficient back pressure for backflushing, such as strand pelletizing. It is also well suited for PET recycling material with a high proportion of contaminants”.