The right combination of technologies to keep the injection process under control
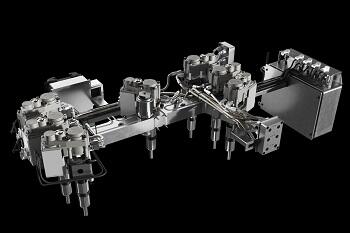
What are the main process anomalies that commonly affect injection molders and how to detect them? Try to imagine the most complex part ever: it is a delicate trade-off of polymer selection, processing, part design and mould design. Several elements could affect the injection process, from the issues related to the injection moulding machine to the moulding material, but how to detect them? Thanks to the combination of the right technologies, defects on the moulded parts can be prevented ensuring higher quality output in less time.
One of the main causes of process variability could be related to the injection moulding machine for example: if the injection moulding machine components - such as the screw, the barrel and the check ring - show signs of wear, the injection process could vary significantly. The result is that the inconstancy produced during the injection/packing phase or the material dosage could cause few defects on the moulded parts.
Another element that often affects the injection process is the viscosity variation of the moulding material. The causes of these anomalies? Few times was observed that different batches of plastic material could behave slightly differently during the injection process. In addition, an eventual percentage of recycled material could be one of the causes of process variability.
How to detect these problems, avoiding process drift? Thanks to pressure sensors, it is possible to get a direct feedback of process constancy by monitoring the real polymer status in the cavity. Moreover, it is possible to highlight if some irregular cycles occur, in order to determine which cycle lies outside of a specified tolerance range. Thanks to pressure sensors it is possible to define if the process is gradually going to drift, or rather, when several cycles are getting far from the ideal process.
Using mould based sensors allows for valve gates to be triggered from mould born events and not based on screw position or time. This allows the process to adapt to actual conditions.
The combination of pressure sensors and Flexflow Evo - the HRSflow electrically driven valve gate system - allows to get a precise control over the whole injection process helping to detect the problems related to the moulding material and the injection moulding machine.
The servo driven valve gate technology is designed for the independent adjustment of each valve pin with precise control of stroke and force during opening and closing phases. This solution assures accurate, easy to operate, flexible control of pressures and flow rates at each individual gate providing far superior flexibility and minimizing the process variability.
Pressure sensors together with Flexflow Evo allow to highlight the polymer status in the mould cavity by delaying or bringing forward the opening/closing phase. This combination ensures not only the maximum process reliability and repeatability but also a uniform quality with a minimal scrap.