Industrial 3D printing within everyone's reach and entry in the stereolithography segment
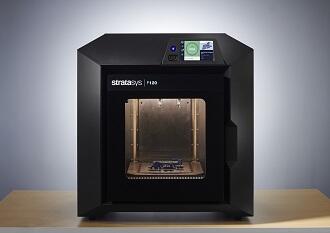
At the Amug (Additive Manufacturing User Group) 2019 conference in Chicago, Stratasys launched two important innovations on April 1: the F120 3D printer, which simplifies the management of additive manufacturing technology by providing reliable and precise complex and functional parts with extreme rapidity, and the V650 Flex printer, which marks the company's entry into the stereolithography segment.
The 123 series enlarges
Setting the stage for a transformation in 3D printing, the new Stratasys F120 3D printer (picture above) is powering the next-generation of designers, engineers, and educators with easy-to-own, industrial-grade additive manufacturing technology. As the newest member of the F123 Series of FDM printers from Stratasys, the F120 brings industrial 3D printing to the masses - backed by simple controls, remote self-monitoring, exclusive 3D printing hardware, and extremely high levels of reliability and repeatability.
The F120 makes it simple even for the novice to get started with 3D printing in the design studio, office or education environments. While it is noted that many desktop 3D printers struggle to produce reliable and accurate parts without technical know-how, the F120 printer is designed to create high-quality FDM models time-after-time. Streamlined plug-and-print functionality removes complexity from typical workflow processes with a user-friendly touchscreen interface and GrabCAD Print workflow.
Allowing for multiple uses in a single system, the F120 can support everything from rapid prototyping and tooling to full manufacturing. With an ability to print up to 3X faster than competitive solutions and tested 24/7 performance, large filament boxes allow for up to 250 hours of uninterrupted printing. Virtually any customer can benefit immediately from the 3D printer’s ease-of-use, high-level accuracy, and hands-free soluble support.
The Stratasys F120 joins the full F123 Series of 3D printers, including the F170, F270 and F370 - combining dependable FDM technology with design-to-print GrabCAD Print software. The solution is available to order starting from its launch, with delivery starting in July.
Stereolithography in cooperation with DSM
Set to disrupt traditional 3D printing, the new V650 Flex stereolithography 3D printer (picture on the right) is the Stratasys entry into the stereolithography segment. This unique offering combines the power of a large-scale system with a configurable environment for fine-tuning across a broad range of resins - giving customers greater accuracy, choice, and lower costs in 3D printed prototype and part development.
Backed by a partnership with DSM, a global, purpose-led, science-based company in nutrition, health and sustainable living, customers have the freedom to capitalize on the quality and high-performance of Somos stereolithography resins with the V650 Flex 3D printer. Available from Stratasys and backed by years of extensive utilization at its service bureau, Stratasys Direct Manufacturing, DSM Somos-verified resins enable customers to produce with confidence - high-quality, durable parts that meet requirements of a wide range of applications.
With a build volume of 50.8 cm (width), 50.8 cm (depth) and 58.4 cm (height) and interchangeable vats, the V650 Flex printer has reliability built-in, with runtime of over 75,000 hours and more than 150,000 parts produced inside Stratasys Direct Manufacturing. The V650 Flex puts the power of verified resins and a configurable system to work - helping customers produce extremely durable, highly complex and accurate parts.
The open vat configuration of the V650 Flex stereolithography printer comes with recipes for DSM Somos resins commercially available directly from Stratasys, including:
- Element, the antimony-free stereolithography resin, specifically designed for producing strong, stable investment casting patterns with fine-feature detail and very low residual burnout ash;
- NeXt, the resin that provides the accuracy of stereolithography with the look, feel and performance of a thermoplastic;
- PerForm, the material-of-choice for applications that require strong, stiff, high-temperature resistant parts, such as tooling and wind tunnel testing;
- Watershed XC 11122, a clear solution for designers looking for ABS and PBT-like properties for stereolithography - producing highly detailed, dimensionally stable, optically-clear parts with water resistance.