High speed assembly of complex products
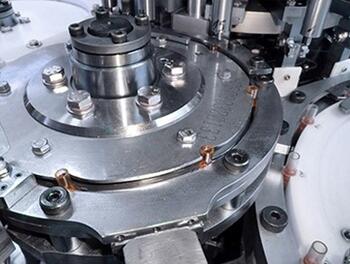
The latest achievement at Gefit headquarter is an assembly cell for a product made of two components, the first made of PC and the second one of soft PVC. The product is a part of the kit for blood transfusions currently used in hospitals.
Accuracy, reliability, special care even for the apparently less important details are the main characteristics of this cell underlined by the manufacturer. Because everyone who uses an assembly machine working at high speed or performing the assembly of complex plastic products, sometimes including several components or made of very different materials, knows very well that even a small detail can have a big impact on a project success. This is a rule that applies to all production fields, but for the medical one it is a primary requirement because of obvious safety reasons and of the extremely high quality standards.
Following this way, Gefit has enhanced its experience in the medical industry, over many years, manufacturing injection moulds and assembly machines, with index or continuous motion technology. This special and dedicated equipment work successfully, for daily production, in several countries all over the world, mostly in clean rooms.
The assembly machine has a compact size and is built on a continuous motion rotary table for a hourly production of 22,000 pieces. The main problem in this assembly process is due to the very specific geometry of the two components and to the plastic resins used in the injection process, particularly for the PVC part. The machine is equipped with upper and lower telescopic spindles as well as special sealing elements for the correct alignment of the parts before the assembly operation. Both components are fed by vibration systems specially designed to better handle the parts inlet onto the auxiliary wheels. To complete the cell, Gefit designers have equipped it with a special vision system, set to read the right position of the PC component before the proper pressing operation.