The final frontier for the beverage industry: extreme productivity and flexibility
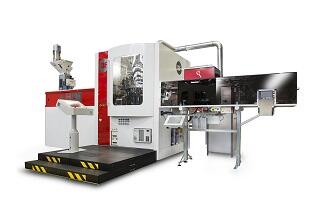
Producing 1,000 caps per minute with just 24 cavities, a cycle time of 1.4 seconds and one of the lowest energy consumption in the sector. Unleashing the full potential of marketing with advanced, flexible, practical digital decoration of caps. These are some of the latest innovations that Sacmi will introduce at K 2016 (Düsseldorf, October 19-26) on the caps and preform manufacturing front.
A pioneer in closure-making compression technology, Sacmi has, over the years, developed incremental innovations, some of which will be previewed at the Düsseldorf fair. Cap digital printing solutions have now reached an even higher level of development and the company is already exploring what some consider to be the final frontier of digital decoration: unlimited colour development, ultra-high definition, yet also extreme flexibility to ensure the right response whatever the customer’s production/promotional needs.
From cap to
pack, Sacmi has harnessed all its compression technology expertise and know-how
to design a completely new plastic container manufacturing platform (highly
interesting applications in the pharmaceutical and dairy sectors will be
presented at the fair), thus mounting a competitive challenge to alternative
technologies thanks to outstanding flexibility, productivity and energy saving.
Also in the
manufacture of PET preforms with injection technology, Sacmi has combined
unparalleled productivity and quality with solutions that ensure maximum
compatibility with existing moulds, thus offering a further competitive
advantage in terms of flexibility. Complete, integrated solutions, designed to
make use and maintenance easier than ever. With one overriding goal: to give
the manufacturer a competitive advantage in terms of efficiency. That’s why
Sacmi has developed and market-launched advanced vision and quality control
systems capable of inspecting every part of the product, identifying any
potential defects and eliminating any risk of line inefficiencies. For the interoperability
and user-friendliness the company has developed an advanced software that is
shared by all Sacmi-designed vision systems, for every stage of primary
packaging production from bottle to closure to labelling.
Visitors to K 2016 can expect all this and more, not to mention the reliability that Sacmi provides in terms of customer assistance, thanks to facilities on five continents, a far-reaching, efficient spare parts service and machines that feature remote control and assistance services accessible from anywhere in the world.