The extrusion made easy
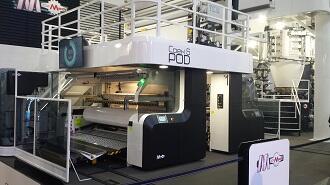
Perhaps not a world record, but definitely Macchi staged a spectacular performance by running, full time, 1,300 kg/h of coextruded, 5-layer flexible pouch laminating grade film.
Nested under the wings of its towering extrusion line, one of the very last releases of the blown film coextrusion high capacity film lines belonging to the POD generation, Macchi recorded over 1,000 presences on its booth. This was arranged around an extremely elegant Italian style setting, recalling the new black and white corporate colour scheme, with an extremely high level of qualified visitors and trade inquiries that generated a large number of sales contracts, even signed on the spot.
As commonly shared comment amongst the world of over 230,000 plastic operators that invaded the German city of Düsseldorf in occasion of the largest plastic show, the 2016 edition collected a general optimistic feeling.
The recently closed trade show came after a 2013 edition which, even if considered by many as the turning point after years of harsh economic recession, had ended as a “let’s wait and see” event, where nobody was willing to bet a coin on the outcomes. The 2016 thus resulted as the “confirmation” show, with solid expectations ahead and no mysteries about a plastic film industry currently in an upswing moment.
Macchi innovations, even if facing lots of trends and
indications of what the industry 4.0 might turn out in the short predictable
future, remain clearly aimed toward a more “traditional” film extrusion
business. Where many examples show that industry 2.0 or 3.0 are still well
alive, and mark a difference from what could be the present reality in the
manufacture of more sophisticated plastic goods. The company’s helm is still
steering to follow a well identified route: flexibility, simplicity, capability.