The development of Tandem regeneration lines keeps on
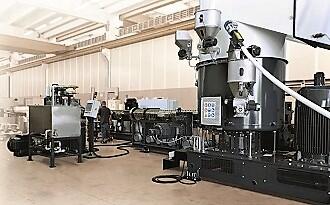
The first half of 2018 was very positive for Gamma Meccanica, Italian company specialized in the production of lines for the regeneration of plastic materials. The recent events NPE and Plast in which the company took place proposing, in particular, the new GM Tandem range of regeneration lines brought many interesting prospects and confirmed the growing interest in this type of technology. The Tandem technology has been developed for many years and recently has been redefined. The most recent systems delivered are the result of continuous technological improvements with a high level of automation, maximum quality of the recycled product (granules) and tremendous energy savings.
Thanks to GM Tandem technology it is possible to recycle heavily printed, highly moist and highly contaminated plastic materials. The line is composed of a Compac unit equipped with the Ecotronic system, a primary extruder, a primary screen changer, a connection neck with a special degassing chamber, a secondary extruder, and, as an option, a second screen changer for finer filtration/purification of the melt and then the pelletizing system. The Ecotronic system, by increasing the number of revolutions above the nominal speed of the motor, allows controlling the temperature without adding water and processing materials with a high percentage of humidity. Ecotronic guarantees a notable energy savings (up to 40%).
An Italian customer has recently installed GM Tandem 160 line for the recycling of milled HDPE. The customer had to recover parts of agricultural plants, in particular irrigation pipes, with high level of contamination from the ground and other residual materials. The material to be recycled is sent to the Tandem regeneration line directly from the washing plant with a humidity rate of approx. 8%. Thanks to the patented and innovative degassing system, 10 times more efficient than traditional systems, humidity is expelled directly during the extrusion phase. The dual filtration up to 100 microns, guarantees the removal of even the smallest parts of contaminants. The production capacity of this Tandem line and with this type of material is 1200 - 1400 Kg/hr. A North American company, instead, purchased a GM Tandem 180 line for the regeneration of PP non-woven, PP raffia bags, BOPP heavily printed film and PE film. These post-consumer and post-industrial wastes have high rate of contaminants like paper, aluminium, PET, PA and sand. In this case the GM Tandem 180 line has the primary extruder with a diameter of 180 mm and the secondary extruder with a diameter of 210 mm and a guaranteed production up to 1500-1700 kg/h.
Given the growing interest of recyclers for the Tandem lines, Gamma Meccanica is developing new models. The next line that will be manufactured is the GM Tandem 210, composed of two extruders, with diameters of 210 and 250 mm, and with a production capacity starting from 2000 kg/h.
Gamma Meccanica has always been aware of the importance of recovering such a precious resource as plastic. For this reason, in addition to offering lines for the regeneration of plastics with growing performances, it is participating, together with a group of Italian companies operating for many years in the recycling machinery field and the European association of plastic recyclers (PRE), at the project "Are you R”. This aims to raise awareness amongst European people on the importance of plastic recycling. The goal is to spread the culture of recycling. Through a number of documents, photographs and funny animation films, the project reveals the advantages of plastics and explains how its impact on the environment could be reduced if correct behaviors were maintained. This will be one of the topics of the "Packaging and Recycling" convention, to be held in Milan on September 26-27 and sponsored by Gamma Meccanica itself.